Üretim planlaması hem PP’de hem de PP/DS’te aynı temel ilkeleri izlemektedir. PP/DS’de üretim planlaması, SAP ERP sistemi ile aynı prosesleri kullanır. Ana veri kayıtlarına, özellikle üretim yerleri, malzeme ana verileri, ürün ağaçları (BOM), işyerleri, iş planları (PP’de) veya planlama reçetelerini (PP-PI’de) esas alınır. Planlama sonuçları planlı siparişler olup üretim gerçekleştirmek için üretim emirlerine dönüştürülür. Bunlar üretim siparişleri (PP’de) veya proses siparişleri (PP-PI’da) olabilir. Üretim, planlı siparişlere dayalı olarak yürütülen Seri Üretim (Repetitive Manufacturing – REM) de mümkündür.
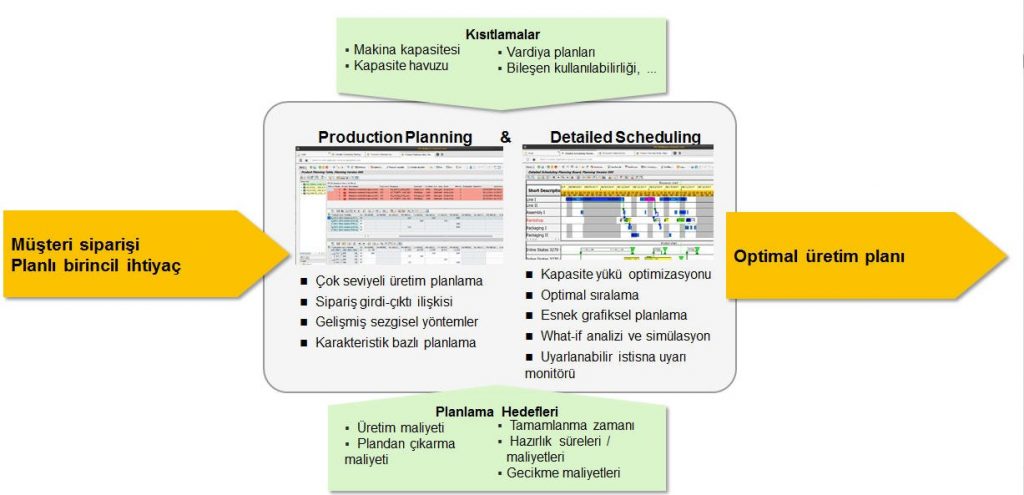
PP/DS modülü PP ana verilerini kullanarak (iş planı, ürün ağacı, kapasite tanımları, çalışma saatleri, vardiya tanımları, hazırlık matrisleri gibi…), yapılacak operasyonların üretim kaynakları üzerine sonlu olarak yerleştirilmesi, sıralanması ve çizelgelenmesi işlemlerini gerçekleştirmektedir. Bu işlemleri çeşitli heuristik yöntemlerle yapabildiği gibi, maliyet minimizasyonu mantığı ile çalışan optimizasyon yöntemlerini de kullanabilmektedir. PP/DS’in en önemli işlevlerinden olan çizelgeme optimizasyonunda amaç sisteme tanımlanacak farklı ürün grupları arasındaki imalat geçiş sürelerini (hazırlık) minimize etmek veya talebi zamanında karşılamaya çalışan bir çizelgeleme sonucu ortaya çıkarmaktır. Bunun için kullanılan optimizasyon genetik algoritma mantığına göre çalışmaktadır.
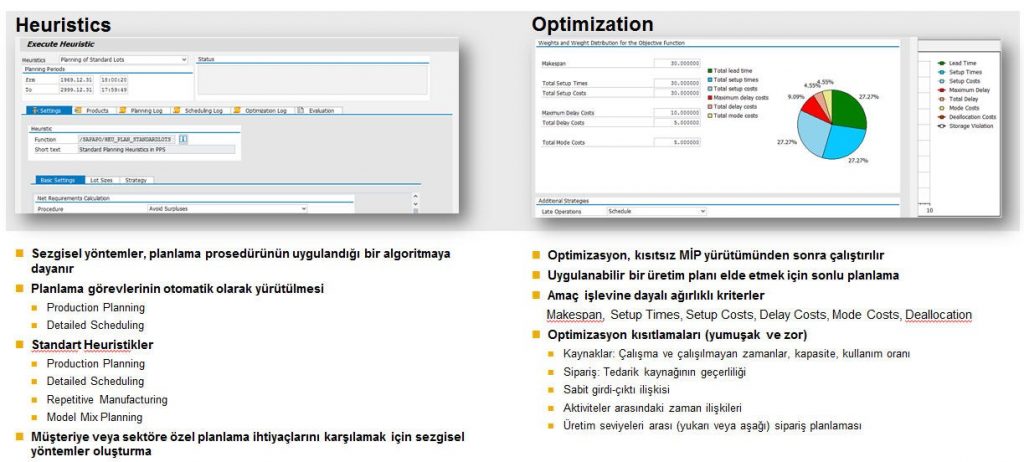
Bu yazıda, PP/DS’de bulunan gelişmiş planlama temel ilkeleri ve işlevleri ele alınmıştır. PP/DS son derece geniş bir yelpazede ek işlemler ve seçenekler sunmaktadır. En temel anlamda kullanılabilecek tüm fonksiyonların aynı anda uygulanması zorunlu değildir. Nitekim, temel süreçlerin kademeli bir şekilde geliştirilmesi genellikle daha kullanışlıdır. Gelişmiş planlama seçeneklerinin aşağıdaki açıklaması özet niteliğindedir.
Gerçek Zamanlı İhtiyaç Planlaması
SAP ERP’de ihtiyaç planlaması gün bazında gerçekleştirilmektedir. Satış siparişlerinde kesin bir teslim edilebilirlik tarihi girebilseniz bile, ihtiyaç planlaması sadece günü dikkate alır. Benzer şekilde, ihtiyaç planlaması yalnızca bir operasyonun tam başlama zamanından türetilen ikincil ihtiyaçların tarihlerini gün olarak hesaba katar. Bu nedenle, aynı tarihin sabah ve öğleden sonraki iki ihtiyacını birbirinden ayırmak olanaksızdır. SAP ERP’deki ihtiyaçları karşılamak üzere oluşturulmuş siparişler yalnızca bir günü içerir.
Bununla birlikte, PP/DS’de, ihtiyaç planlaması gerçek zamanlara dayanmaktadır (saniyeye kadar). Satış siparişleri, ikincil ihtiyaçlar ve diğer tüm ihtiyaçlar için kesin bir zaman atanır. İhtiyaçları karşılamak için oluşanacak tedarik önerilerinin tam da bu saatte yapılması planlanmaktadır.
Eşzamanlı Miktar ve Kapasite Planlaması
SAP ERP’de, miktarlar ve kapasiteler ayrı ayrı planlanır. Bu, ihtiyaç planlaması için de geçerlidir, ancak bir siparişi manuel olarak oluşturduğunuzda veya değiştirdiğinizde, kapasiteleri dikkate alma olasılığı da benzer şekilde sınırlıdır ve bunun ikinci bir adımda yapılması gerekir.
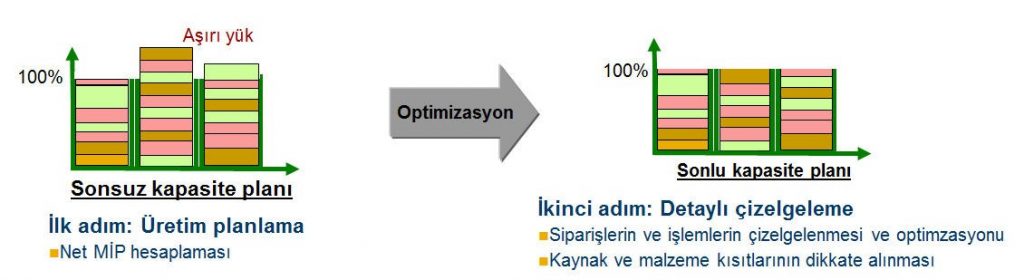
PP/DS’de, aynı anda miktar ve kapasiteyi planlayabilirsiniz. Örneğin, kapasite durumu, kapasite planlamasının halihazırda tamamlanmış olduğu ve üretim planının zaten oluştuğu kısa vadeli ufukta ilave bir sipariş oluşturulduğunda da dikkate alınır. Sipariş, yalnızca sıradaki işlemler için mevcut kapasite bulunursa oluşturulabilir ve daha sonra otomatik olarak bu süre zarfında planlanır. Eşzamanlı malzeme ve kapasite ihtiyaç planlaması için kaynakları sonlu kaynaklar olarak tanımlayabilirsiniz (planlama için kritik olan kaynaklar). Bu kaynaklarda, planlı siparişler/üretim siparişleri yalnızca sipariş tarihinde sipariş miktarı için yeterli kapasite varsa oluşturulur. Eğer yeterli kapasite yoksa, sistem kapasite durumunu dikkate alarak yeni bir tarih arar.
Üretim Planlaması Çalışması (Çok Adımlı)
PP/DS’de, otomatik üretim planlama sürecini birkaç adımdan oluşturmak kolaydır. Bireysel adımlar, üretim planlama çalışmasında belirtilir. Bireysel adımların mantıksal bir sıraya nasıl yerleştirilebileceğine ilişkin bir örnek olarak:
1. MİP mantığını temel alan ihtiyaç planlaması
2. Darboğaz kaynakları için kapasitelerin planlanması
3. Kapasite planlamasının sonucu ihtiyaç tarihleri değişen malzemelerin ihtiyaç planlaması
Bu adımlar, heuristik yöntem olarak adlandırılan prosedürler kullanılarak kolayca tanımlanabilir ve spesifik malzemeler veya kaynaklar ile sınırlanabilir. Bu tür bir planlama çalışmasının sonucu (pratikte genellikle en fazla 10 adımdan oluşur), olası birçok planlama koşulunu (örn. kapasite darboğazları) mümkün kılan bir tedarik planıdır.
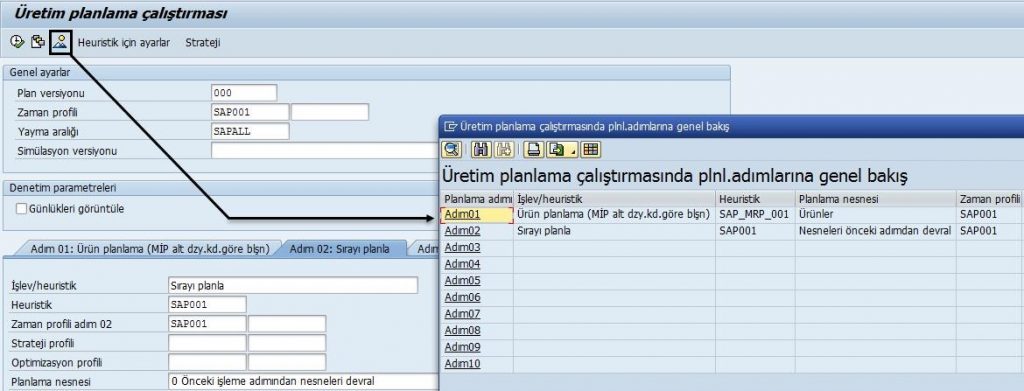
Planlı birincil ihtiyaçlar PP/DS’deki üretim planlamasının başlangıç noktasıdır. Planlamada mevcut lokasyonlardaki stoklar da dikkate alınır. Otomatik planlamanın belirli bir ürün için geçerli olup olmadığı ürünün PP/DS sekmesinde ayarlanabilir. Ürünler planlama çalıştırması ile planlanacak ise, sıralamada belirtilen heuristik yöntemleri kullanılır. Bu aşamada kendi heuristik yöntemlerinizi veya SAP tarafından sağlanan heuristik yöntemleri kullanabilirsiniz. Çeşitli parti büyüklüğü heuristik yöntemleri ve satınalma sipariş miktarı optimizasyonu da dahil olmak üzere, belirli planlama sorunlarını ele alan ürünleri planlamak için çok çeşitli heuristikler mevcuttur. Bir ürün lokasyon için planlama prosedürü olarak “planlama çalışması” seçildiğinde, planlama ile ilgili bir olay meydana geldiğinde bir planlama dosyası girişi oluşturulur (örn. ihtiyaçların veya stoğun değiştirilmesi). Bu ürünler daha sonra bir sonraki net değişim planlama çalışmasında planlanır. Hemen planlama ile karşılaştırıldığında, üretim planlama çalıştırmasında ürünü planlamanın avantajı, ürünlerin ne zaman ve ne sıklıkta planlandığını kontrol edebilmenizdir. Böylece, daha yoğun olmayan zamanlarda planlama çalıştırmalarını gerçekleştirerek sistem performansını artırabilmenize olanak tanır.
Malzeme Akışında Girdi-Çıktı İlişkisi ve Kontrolü
SAP ERP’de, ihtiyaç planlamasını değerlendirmek için tedarik unsurları arasında dinamik referanslar oluşturulur. Bu referanslar MİP listesinde veya güncel stok/ihtiyaç listesinde sipariş raporu veya ihtiyaç listesi işlevlerinin bir parçası olarak görülebilir ve planlama sonucunu manuel olarak düzenlemek için kullanılabilir. Bu ilişkiler dinamik olarak oluşturulduğundan ve veritabanında depolanmadığından diğer işlemler veya işlevler için kullanılamaz.
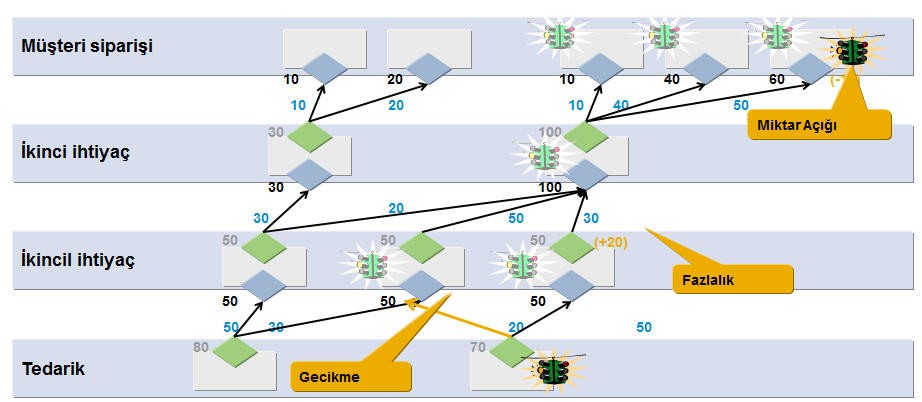
PP/DS’de, ihtiyaçların planlaması veya siparişlerin oluşturulmasından sonra ihtiyaçlar ve tedarik unsurları arasında benzer şekilde dinamik referanslar yaratılmıştır. PP/DS’te bu referanslara girdi-çıktı (pegging) ilişkileri denir. Bu ilişkiler tüm ürün ağacı seviyelerinde çok seviyeli üretimde oluşturulmuştur. Bu ilişkiler ağı bir girdi-çıktı ilişki ağı olarak anılır. SAP ERP’nin aksine, girdi-çıktı ilişkileri PP/DS veritabanında saklanır ve PP/DS’teki diğer uygulamalarda kullanılabilir. Örneğin, kapasite planlamasında sipariş değiştiğinde bileşenlerin ilgili siparişlerini kaydırmak için kullanılabilir.
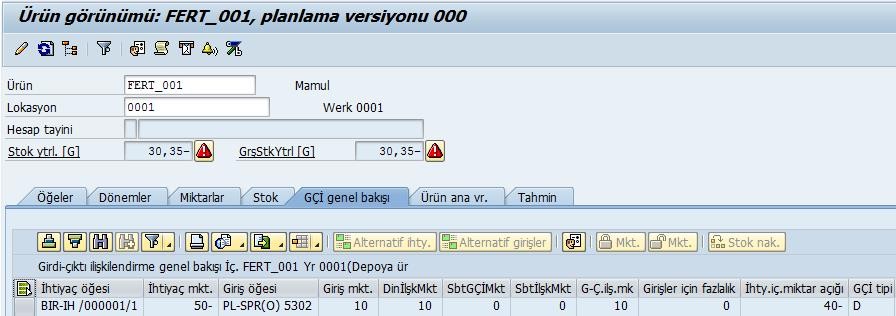
Sipariş değişikliklerinin iki yönlü yayılımı yine bu sayede sağlanır. Siparişlerde, örneğin bitmiş ürün seviyesinde zamanla ilgili değişiklikler yaparsanız, sistemin yarıürün siparişlerini otomatik olarak hareket ettireceğini belirtebilirsiniz. Bununla birlikte, yarıürün siparişleri için yeterli kapasite yoksa, istisna iletisi üretilebilir veya sipariş bitmiş ürün seviyesinde taşınmayabilir.
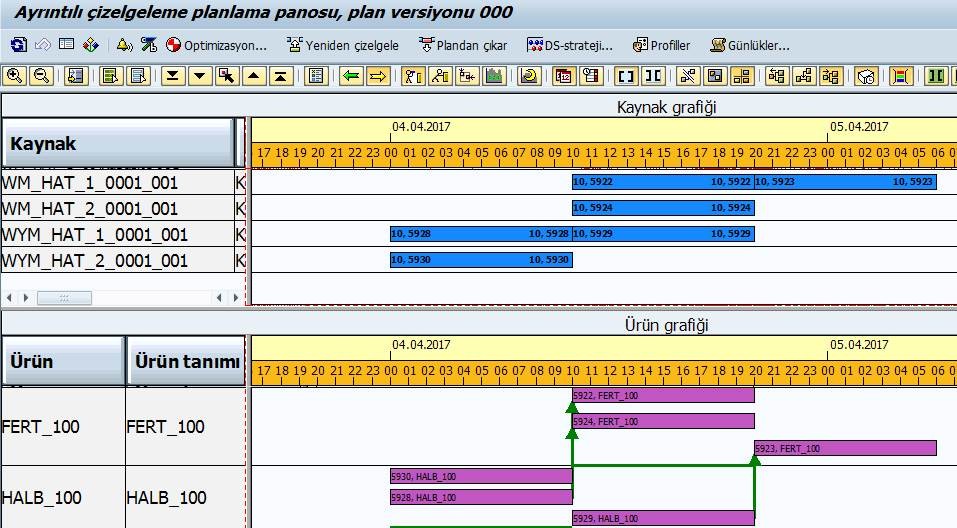
Tedarik Kaynağı Belirleme ve Maliyet Bazlı Planlama
Şirket içinde üretilen malzemeler için alternatif üretim versiyonları olarak çeşitli tedarik kaynakları da mevcut olabilir. Bu noktada, üretim versiyonlarını kullanımı PP/DS için en önemli bilgi haline gelmektedir. Üretim versiyonları genellikle bir ürün ağacı ve bir iş planı (veya PP-PI’de planlama reçetesi) belirleyerek hangi üretim sürecinin kullanılacağını tanımlar. Üretim versiyonları, geçerlilik tarihleri ve parti büyüklüğü aralığı bakımından sınırlandırılabilir. Birden fazla geçerli üretim versiyonu aynı anda mevcutsa, SAP ERP ilk geçerli versiyonu basitçe seçer ya da üretim miktarını çeşitli üretim versiyonlarına dağıtmak için bir kota düzeni kullanılır.
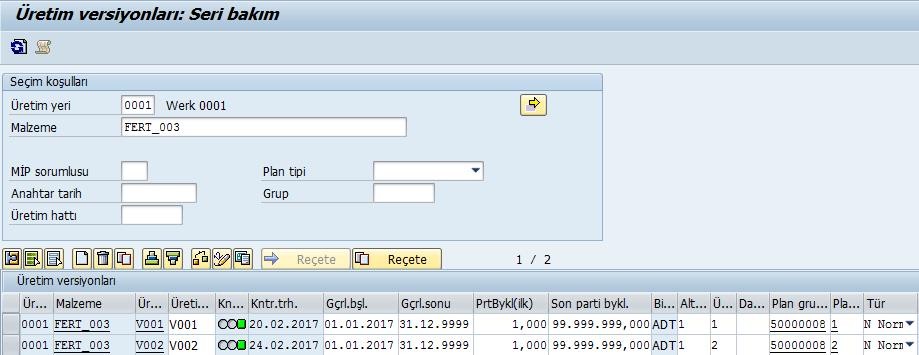
Üretim versiyonu PP/DS’e aktarıldıktan sonra üretim verileri yapısı (PDS-Production Data Structure) adını alır. Bununla birlikte, bir tedarik kaynağı seçme süreci PP/DS’te genellikle farklıdır; burada maliyetler çok önemli bir rol oynayabilir.

Dışarıdan tedarik senaryosunda belirli bir tedarik kaynağının gerekli teslim tarihine kadar teslim edip edemeyeceğini belirlemek için bir kontrol gerçekleştirilir. Tedarik süresinin çok uzun olması nedeniyle bu mümkün değilse, PP/DS daha kısa bir teslimat süresi ile alternatif bir tedarik kaynağı arar. Örneğin, zamanlama sorunları ortaya çıkarsa, en kısa teslimat süresine sahip satıcı seçilebilir. Ayrıca, tedarik ile ilgili olarak maliyetler düşünülebilir. Birkaç olası satıcı arasından planlamanın, en düşük masrafa sahip olanın planlanmasının daima otomatik olarak seçilmesini (herhangi bir zamanlama problemi bulunmaması koşuluyla) yapabilirsiniz. Bu durumda, çeşitli fiyat ölçekleri dikkate alınabilir. Böylece, parti büyüklüğüne bağlı olarak farklı satıcıların kullanılabileceği anlamına gelir.
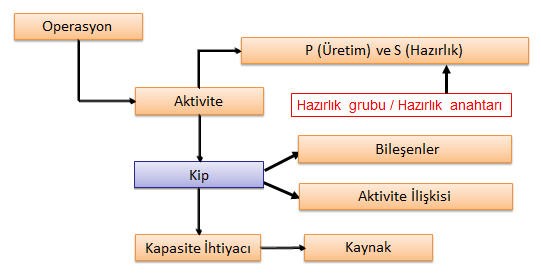
Süreç, dahili üretim planlaması için tamamen aynıdır. Çeşitli üretim versiyonlarında (üretim veri yapıları olarak PP/DS’e aktarılan) üretim süreleri ve üretim maliyetleri açısından farklılıklar olabilir. Sistem bu alternatifler arasından en uygun olanını seçmeye çalışır. Alternatif kaynakları planlamak ise bir kaynakta yeterli kapasite yoksa, operasyon alternatif kaynaklara (alternatif kip olarak) yeniden düzenlenebilir.
Gelişmiş Uyarı İzleme
İstisna iletileri (uyarılar) planlamayla ilgili sorunları gösterir. SAP ERP’de, istisna iletileri MİP listesinde veya güncel stok / ihtiyaç listesinde görüntülenir. Tüm MİP listelerini toplu ekranını çağırırsanız toplu değerlendirme yapmak mümkündür. Malzemeye genel bakışta, ayrı malzemede görünen ve istisna grubuna göre sıralanan istisna mesajları görüntüleyebilirsiniz. Bir sorunu incelemek için, ayrı listeye erişmeniz gerekir.
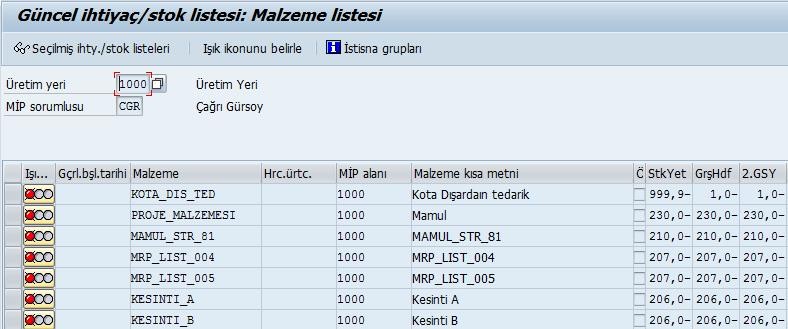
PP/DS’de uyarı yönetimi seçenekleri SAP ERP’den çok daha gelişmiştir. Uyarıları değerlendirme listelerinde (örneğin, sipariş görünümlerinde) birçok farklı şekilde gösterebilirsiniz. Buna ek olarak, önemli bir bileşenin tedariğiyle bağlantılı olarak verilen uyarılar da bitmiş üründe görüntülenebilir (ağ uyarıları). Uyarılar ilgili girdi-çıktı ilişkilerine dayalı olarak yayılabilir. Girdi-çıktı ilişkisi ağı siparişler için sipariş yapısının tamamını değerlendirmek için de kullanılabilir. Etkileşimli planlama sırasında, dinamik istisnai mesajlar aracılığıyla destek sağlanabilir (planlama sonuçlarını kaydetmeden de gerçekleşir) ve bu da bir “uyarı temelli planlama” sağlar.
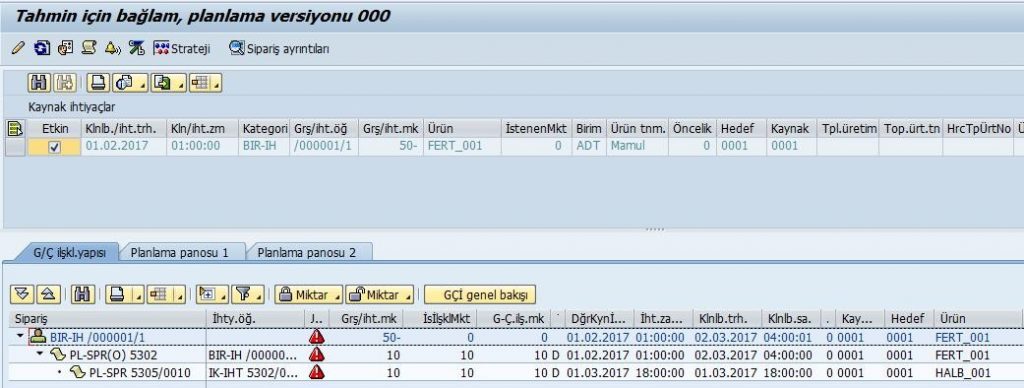
Son olarak, uyarı monitörü, uyarıların merkezi olarak değerlendirilmesi için kapsamlı bir araç sağlar. Uyarı monitörü, ilgili tüm uyarılara genel bir bakış sağlar. Uyarılar, tüm malzemeler, kaynaklar, üretim yerleri vb. boyunca değerlendirilebilir. Uyarı monitörünü grafik olarak ürün planlama tablosuna dahil ederseniz, bu bir grafikte manuel değişiklikler yapabilmeniz (örneğin, kapasite planlama tablosundaki siparişleri değiştirmeniz) ve aynı anda uyarı monitörü tablosunda sonuç olarak tetiklenen veya çözülen uyarılar olarak belirir.
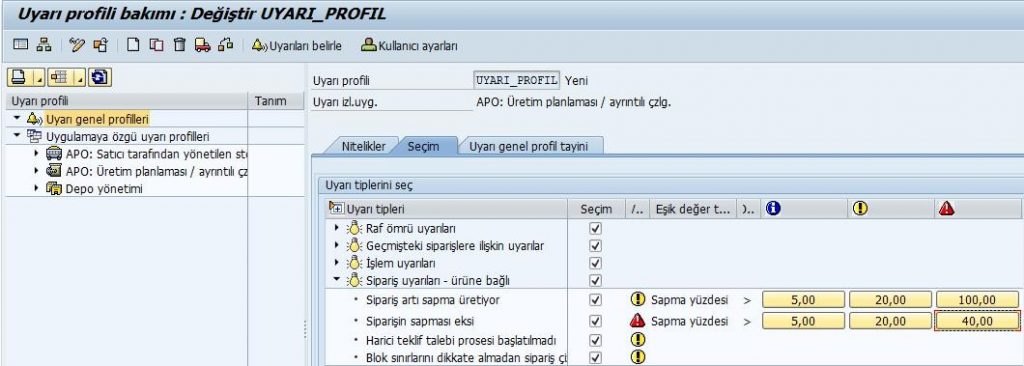
Kapasite Planlamasında İleri Düzey Seçenekler
SAP ERP’de kapasite planlaması manuel olarak (kapasite planlama tablosunda) yapılabilir veya otomatik olarak arka plan işi olarak yürütülebilir. Aynı işyerini gerektiren tüm siparişler kronolojik sırayla planlanabilir. PP/DS’de kapasite planlamasını kullanmanın genel bir yararı geliştirilmiş performanstır. LiveCache mimarisi nedeniyle, PP/DS’teki ayrıntılı çizelgeleme planlama panosu, çalışma zamanını etkilemeksizin birçok sipariş için kullanılabilir. PP/DS’teki oldukça gelişmiş performans, tek tek adımları manuel olarak geri almanıza olanak tanıyan ‘Geri al’ fonksiyonu gibi yeni özelliklerin eklenmesini de sağlar.
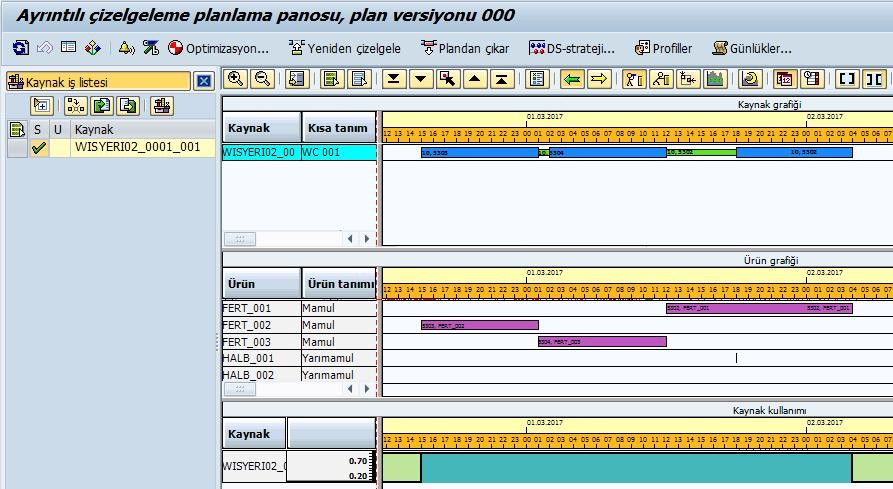
Özellikle siparişlerin otomatik terminlenmesi ve yeniden çizelgelenmesi için bir dizi gelişmiş seçenek ve seçim kriterleri sağlanmaktadır. Aşağıdakileri özellikleri tanımlamak için strateji profilini kullanabilirsiniz:
· Sonlu veya sonsuz çizelgeleme, gerekirse sonluluk seviyesi kullanılır
· Çizelgeleme sırası
· Alternatif kaynakların (kipler) dikkate alınması gerekip gerekmediği
· Girdi-çıktı ilişkilerinin göz önüne alınıp alınmayacağı
· Sipariş iç ilişkilerinin dikkate alınması gerekip gerekmediği
· Kaynak ağlarının dikkate alınıp alınmaması
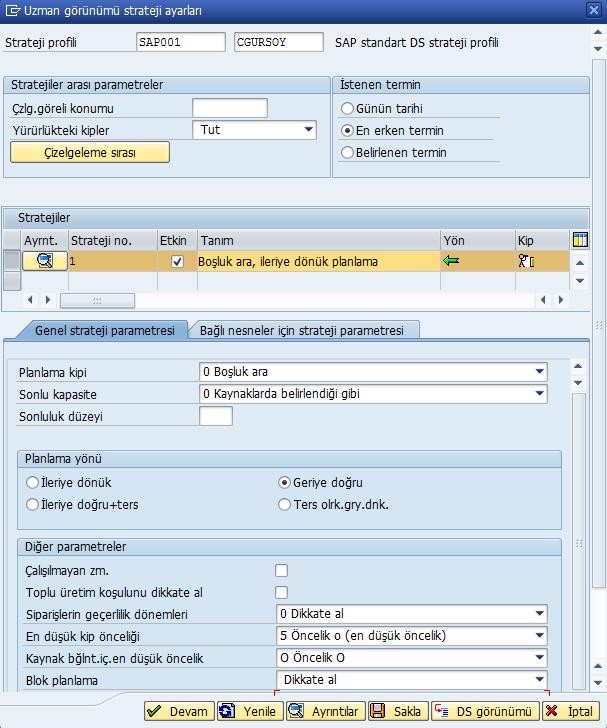
Kapasite planlama için çeşitli işlevler ve heuristik yöntemler mevcuttur, girdi-çıktı ilişkileri grafik şekillerinde kullanılabilir, kaynak aşırı yük uyarıları sorun giderme için kullanılabilir. Tüm bunlar operasyonel veriyi etkilemeyecek şekilde simülasyon versiyonlar aracılığıyla yürütülebilme şansına da sahiptir.
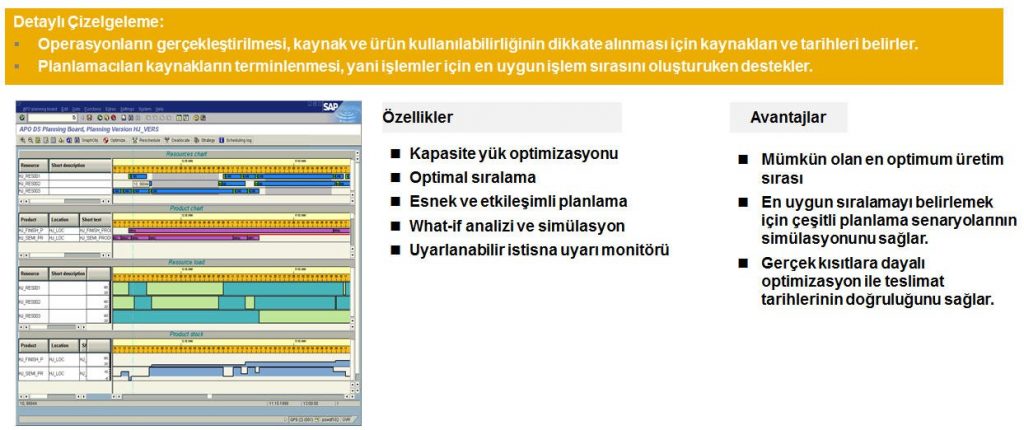
PP/DS Optimizasyonu
PP/DS, güçlü bir optimizasyon aracı olan PP/DS optimizasyon programı içeren bir üretim planlama sistemine sahiptir. Optimizasyon, mantıksal olarak aşağıdaki üç adıma bölünmüş olan üretim planlama sürecindeki son adımdır:
1. İhtiyaç planlaması
2. Kapasite planlaması
3. Optimizasyon
Planlama sırasında, siparişlerin sırasının optimum olmadığı siparişler üretilmiş olabilir. Bu nedenle, optimizasyon çalışmasında mevcut siparişlerin sırasını ve kaynak atamasını değiştirebilirsiniz. Bu nedenle, 2. ve 3. adımlar optimizasyon programı tarafından seçilip birleştirilebilir. Optimizasyon, çok seviyeli bir üretim planında tüm koşulları (kısıtlamaları) sürekli dikkate almak için kullanılır.
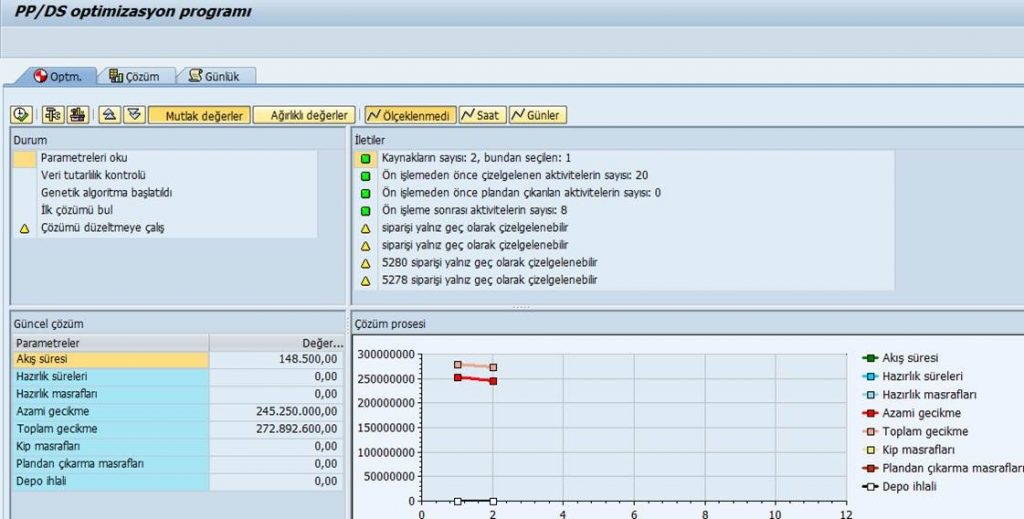
PP/DS optimizasyon programının kullanımı, arka planda planlama çalışmalarına tamamen entegredir. Genellikle optimizasyon, MİP planlamasından sonra çağrılır. PP/DS (DPS01) için optimizasyonu, birden fazla CPU’yu kullanacak şekilde yapılandırılabilir (Multi Agent Optimizasyon). Optimizasyon sırasında, sistem optimizasyon için birkaç işlemciyi (aracı) paralel olarak kullanır.
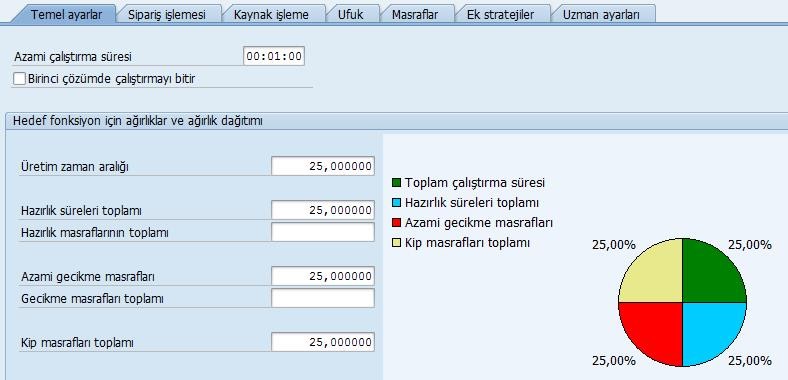
Her bir optimizasyon adımında, nesneler daha önce hedeflenen çözümlerini birbirlerine bildirir ve en iyi çözümleri bulmaya çalışır. Burada çözüm için ağırlıklar (hazırlık süresi veye masrafı, gecikme süresi masrafı vb.) belirlenebilir. Veri hacmine ve optimizasyon senaryosuna bağlı olarak, PP/DS optimizasyonun performansı ve sonucu farklı olmaktadır.
Özel İşlevler ve Heuristik Yöntemler
SAP ERP’de planlamayla ilgili kesin adımlar bir dizi özelleştirme ayarları tarafından belirlenebilir. Bununla birlikte, işleri daha da ileri götürmek ve örneğin yeni planlama algoritmaları oluşturmak istiyorsanız, SAP ERP sisteminde çeşitli değişikliklerin yapılması gerekir. PP/DS’de, sisteme ek fonksiyonlar veya heuristik yöntemler ekleyerek yeni algoritmaları ve süreçleri planlama sürecine dahil etmek çok kolaydır. Standart algoritmaların yanı sıra kullanıcı tanımlı heuristik yöntemler uygulanabilmektedir. Uygulamalarda alternatif olarak heuristiklerin içeriği değiştirilerek planlama yöntemlerinin çeşitliliği arttırılabilir.
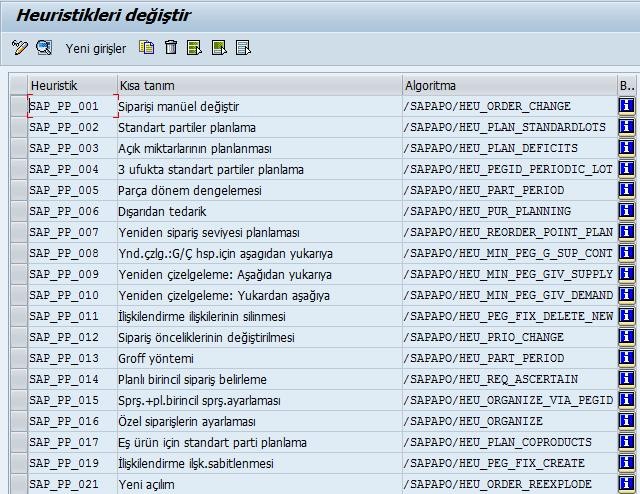
PP/DS’te sezgisel yöntemler temelde iki farklı kapsamda ele alınır. Bunlar, PP heuristikleri ve DS heuristikleri olarak kategorize edilebilir. Sistemde 80’e yakın heuristik bulunmaktadır. (Not: APO-PP/DS ile S/4HANA-PP/DS heuristik yöntemleri farklılık gösterebilir)
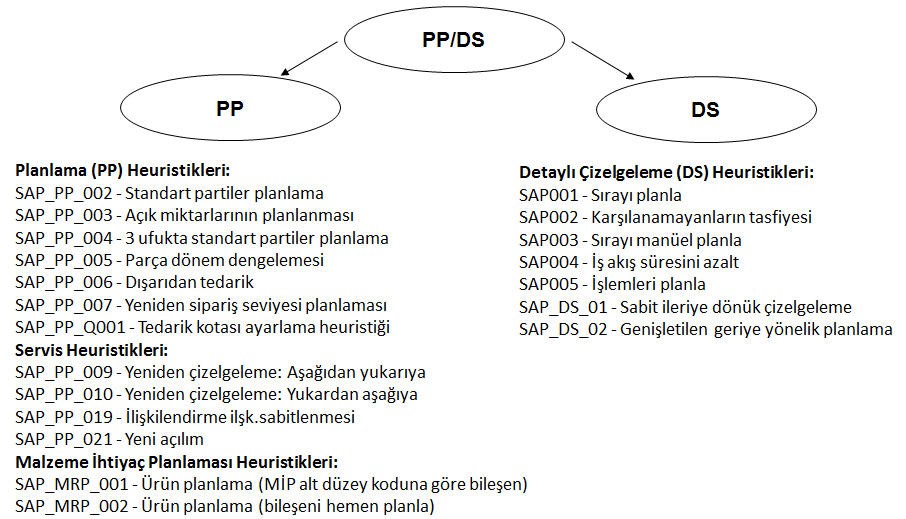
Karakteristik Bazlı Planlama (Characteristics Dependent Planning)
Tedarik öğesini benzer karakteristik değerlere sahip talep ile eşleştirir. Bileşenleri, özelliklerine dayalı olarak malzeme ürün ağacında yapılandıran nesne bağlantılarına göre planlar. Sınıflandırmaya göre planlama becerisine sahiptir. Kaynaklar üzerinde terminlemede karakteristik bazında kısıtlamayı destekler.
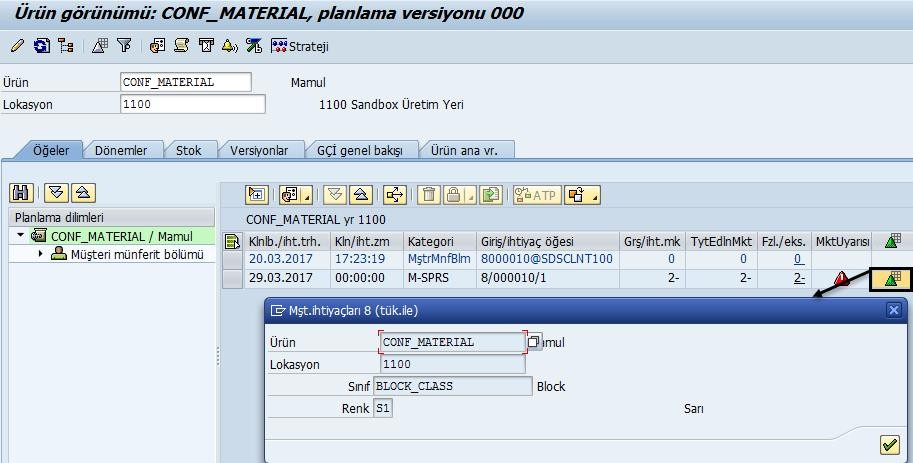
Karakteristikleri temel alan üretim çizelgeleme, planlayıcının, hazırlık süresini en aza indirgemek için kaynaklar üzerindeki işlemleri sıralamasına olanak tanır. Ürün özelliklerine dayalı kaynak kapasitesinin akılcı ve verimli bir kullanım şeklidir. Çeşitli model karışımları ile kısıtlamaya dayalı sıralamaya olanak sağlar.
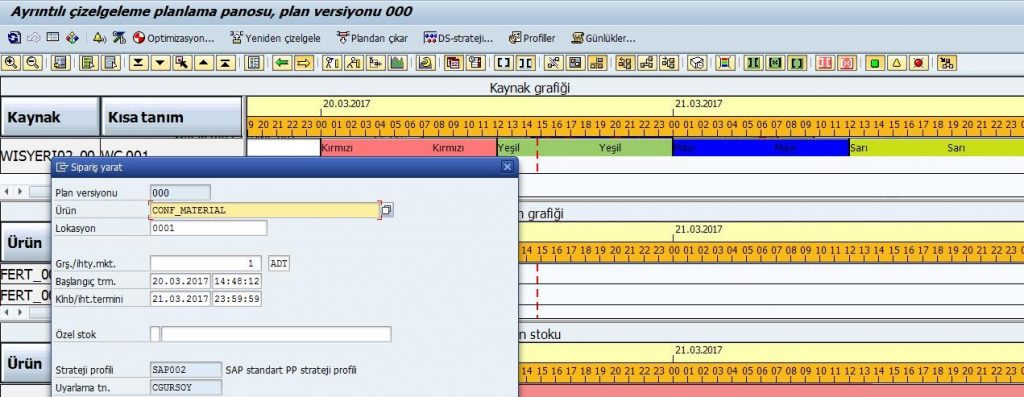
Burada kapasite üzerinde belirli bir karakteristik değerleri için tanımlı olan periyot kullanılarak karakteristik değerine sahip tedarik önerisinin ilgili aralıkta planlaması (blok planlama) sağlanabilmektedir.