PP/DS – Üretim Planlama ve Detaylı Çizelgeleme ürünü kısa dönemli planlama için en iyi çözümdür. APO-PP/DS’den sonra S/4HANA üzerinde yer almaya başladı ve temelde üretim verimliliğini en üst düzeye çıkarmayı amaçlamaktadır. Planınızı optimize ederken, ürün ihtiyaçlarını karşılamak için tedarik önerileri yaratır. Sınırlı kapasite planlama özelliği ile şirketlerin ne zaman, nerede ve ne yapacaklarını belirlemeye yardımcı olur. Üretim Planlama ve Detaylı Çizelgeleme (PP/DS) modülünün en temel özelliği:
· Ürün ihtiyaçlarını karşılamak için dahili üretim veya dışarıdan tedarik önerileri oluşturmak (PP)
· Kaynak çizelgelenmesini ve sipariş tarihlerini/terminlerini ayrıntılı olarak optimize etmek ve planlamak (DS)
Kaynak ve bileşen kullanılabilirliğini dikkate alabilirsiniz. Her şeyden önce, PP/DS, uzun yenileme süreleri olan ürünler veya darboğaz kaynaklarında üretilen ürünler gibi kritik ürünleri planlamak için kullanılır. PP/DS’i sağlıklı üretim planları oluşturmak için kullanabilirsiniz. Böylece, teslimat sürelerini azaltarak ve zamanında teslimat performansını arttırabilirsiniz. Kaynakların, üretimin ve tedariğin daha iyi koordine edilmesi yoluyla ürünlerin verimliliğini arttırın ve stok maliyetlerini azaltın. Ayrıca, beklenmeyen etmenleri yönetmekte size yardımcı olur:
· Müşteri siparişini iptal ederse
· Tedarikçi kaynaklı problemler ve geciken dışarıdan tedarikler
· Makine arızası
· Proses beklenenden fazla ıskarta veriyor ise
PP/DS üretim ilişkili parametreleri dikkate alarak optimum planın çıkmasını sağlar:
· Kaynak kapasiteleri
· Malzeme kısıtları
· Üretim lokasyonlarına özel üretim kısıtları
· Stok hedefleri ve periyodik planlama kısıtları
PP/DS üretim çizelgeleme ile üretim kaynakları üzerindeki işlerin;
· Önceliklere ve termin tarihlerine uygun olarak,
· Kapasite ve malzeme kısıtlarını dikkate alarak,
· Hazırlık ve geçiş sürelerine harcanan zamanı minimize ederek,
· Sıralama kısıtlarını dikkate alarak çizelgelenmesini sağlar.
Üretim planlama ve detaylı çizelgeleme (PP/DS), gelişmiş planlama ve optimizasyon araçları ile kapasite planlamacılarının işlerini daha iyi yapmalarına yardımcı olabilir. Ama nasıl?
Optimization
Optimizasyon aracını kullanarak, planlama durumunu iyileştirmek ve belirli detaylı çizelgeleme sorunlarını çözmek için kaynak üzerinde hazırlık zamanları ve hazırlık maliyetleri gibi belirli ölçütlere göre optimize edebilirsiniz.
Optimizasyon tarihleri, kaynakları ve aktivitelerin sırasını, amaç fonksiyonuna dayanarak değerlendirir. Amaç, ağırlıklı zaman ve maliyetlerin (optimizasyon kriterleri), özellikle çizelgeleme için kritik öneme sahip olan toplamıdır. Optimizasyon sırasında, sistem amaç fonksiyonun değerini azaltmaya çalışır; yani, ağırlıklarına göre çeşitli zamanların ve maliyetlerin mümkün olduğu kadar düşük olduğu bir çözüm bulmaya çalışır. Genel olarak, tüm çizelgeleme hedeflerini aynı derecede yerine getirmek mümkün değildir. Örneğin, hazırlık süresinde bir azalma, gecikme süresinde bir artışa yol açabilir.
İyi sonuçlar elde etmek için kullandığınız optimizasyon kriterleri, planlama durumuna ve kurumsal hedeflerinize bağlıdır. Çözümün kalitesini, optimizasyona izin verdiğiniz işlem süresi üzerinden kontrol edebilirsiniz. Temel kurallar şunlardır:
· Ne kadar uzun süre kullanılırsa, çözüm o kadar iyi olur.
· Sorun ne kadar kapsamlı ve karmaşık olursa, gereken süre o kadar artar.
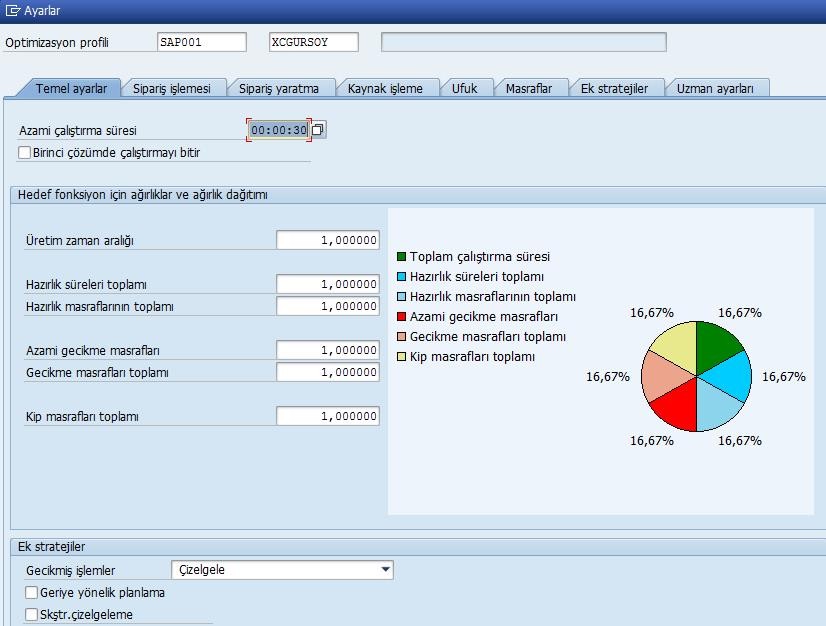
Delay Cost
PP/DS optimizasyonunu siparişlerin veya işlemlerin gecikmeli tamamlanmasıyla ilişkili maliyetlere göre optimize etmek için kullanabilirsiniz. Aşağıdaki optimizasyon kriterleri mevcuttur:
· Optimizasyon ufku içindeki gecikme maliyetlerinin toplamı
· Maksimum gecikme maliyeti
Ne zaman bir gecikme oluşur?
· Giriş tarihi / saati, zorunlu tarih / saatten daha geç ise
· Bir aktivite için izin verilen yeni başlangıç veya bitiş tarihi / saati gerçek başlangıç veya bitiş tarihi / saatinden önce ise
Sipariş önceliği ve gecikme süresi, tek bir siparişin veya aktivitenin gecikmesinin ne kadar olacağını belirler. Aşağıdaki şekilde hesaplanır:
Gecikme maliyetleri = Öncelike bağlı maliyetler x Saniye cinsinden gecikme süresi
Sipariş önceliğine bağlı olarak önceliğe göre maliyetler optimizasyon profilinde tanımlanır.
Mode Cost
Aynı sınıflandırmaya sahip iş yerleri için alternatif kipler oluşturulmaktadır. Bir işlemi belirli bir kaynaktan diğerine geçirmek için alternatif kipler kullanılır. İş yeri sınıflandırılması ardından iş planında operasyonların sınıflandırılması, entegrasyon sonrası PDS’de bir aktive (örneğin üretim aktivitesi) tarafından kullanılan kipler haline gelecektir.
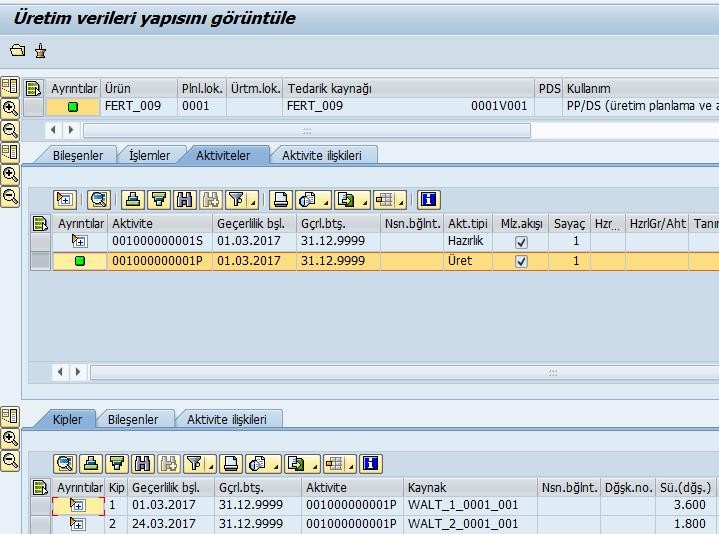
PP/DS optimizasyonunu aktiviteler için kip maliyetlerinin toplamına göre optimize etmek için kullanabilirsiniz. Bir aktivite için kip maliyetleri, belirli bir kipte bir işlem yürütülürken ortaya çıkan maliyetlerdir. Sabit ve değişken maliyetler aşağıdaki gibi hesaplanır:
Kip maliyetleri = Sabit maliyetler + Değişken maliyetler x Saniye cinsinden aktivite süresi
Kip önceliğine bağlı olarak sabit ve değişken maliyetler optimizasyon profilinde tanımlanır.
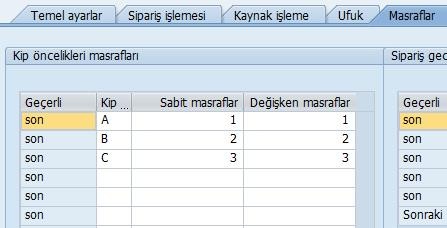
Setup Cost
PP/DS optimizasyonunu toplam hazırlık sürelerini ve maliyetlerini azaltarak, kaynak (tekil kaynak veya tekil karma kaynak) kullanımını optimize etmek için kullanabilirsiniz. Sistem, hazırlık zamanını ve hazırlık matrisindeki sıraya bağlı hazırlık maliyetlerini belirler.
Eğer darboğaz kaynağının hazırlık problemi önemli değilse siparişleri planlamak genellikle basit bir işlemdir. Bununla birlikte, tek tek işlemlerin işleneceği hazırlık süreleri önemli bir optimizasyon potansiyeli olarak eklenirse, yani hazırlık matrisleri kullanılıyorsa ve bir üretim programında toplam hazırlık süresi büyük oranda zaman çizelgesine bağlı hale gelir. Hazırlık koşullarına bağlı değişimler, çoğu durumda PP/DS optimizasyonu ile planlamanın en etkili aracıdır. PP/DS optimizasyonu aynı anda birkaç kısıtı hesaba katmak için kullanabilirsiniz; sipariş öncelikleri dahil edilebilir ve çok seviyeli bir optimizasyon mümkündür.
PP/DS Optimization Order Creation
Sipariş oluşturma işlevselliği APO-PP/DS Optimizasyonu tarafından sağlanmaktadır. PP/DS optimizasyonu, yalnızca siparişleri yeniden düzene koymak yerine sipariş oluşturmak için kullanılabilir. Böylece, tek adımda üretim planlama ve çizelgeleme yaparak planlama döngüsünü basitleştirin.
Storage Cost
Depo masraflarını dikkate alarak çizelgeleme yapılması PP/DS optimizasyonu ile mümkündür. Bu amaçla ürün ana verisinde, ürün depo masrafı tanımlanır. Optimizasyon profilinde depo masrafları toplamı katsayısı belirlenir.
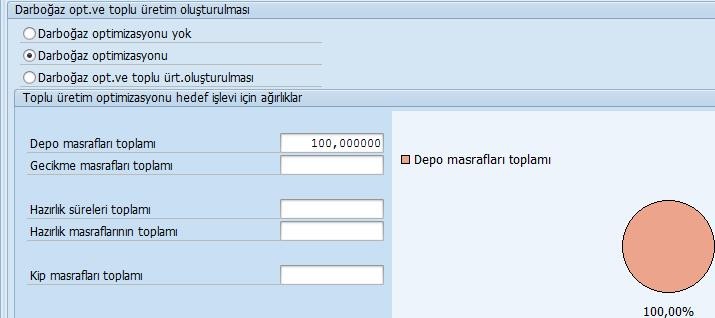
Heuristic
Şirketlerin büyük bir çoğunluğu PP/DS optimizer kullanmamaktadır (ya sezgisel yöntemleri kullanırlar ya da hiçbir yöntem kullanmazlar, sadece planlamacılar işleri kaynaklara manuel olarak taşır). PP/DS aslında çok geniş bir çeşit sezgisel yöntemlere sahiptir. Birçoğu sadece belirli üretim tiplerine yönelik (örneğin, Seri üretim heuristikleri) olan geniş çeşitlilikteki sezgisel yöntemler, PP/DS için muhtemelen en güçlü noktadır. Çoğu PP/DS projesi, sezgisel yöntem ve bunların sıralamasını birleştirerek üretim sürecinin özel gereklilikleriyle eşleştirir.
Heuristik, problem çözme, öğrenme ve keşfetmeye yardımcı olan deneyime dayalı teknikler için bir sıfattır. Sezgisel yöntem, mümkün olan en iyi cevaba veya optimum çözüme yakın olması beklenen bir çözüme hızla ulaşmak için özellikle kullanılır. Daha kesin bir ifadeyle, sezgisel tarama, insanlar ve makinelerde problem çözmeyi kontrol etmek için kolayca erişilebilir ve bilgiyi kolayca kullanabilen stratejiler anlamına gelir.
PP/DS’te sezgisel yöntemler temelde iki farklı kapsamda ele alınır. Bunlar, PP heuristikleri ve DS heuristikleri olarak kategorize edilebilir. Sistemde 80’e yakın heuristik bulunmaktadır. (Not: APO-PP/DS ile S/4HANA-PP/DS heuristik yöntemleri farklılık gösterebilir)
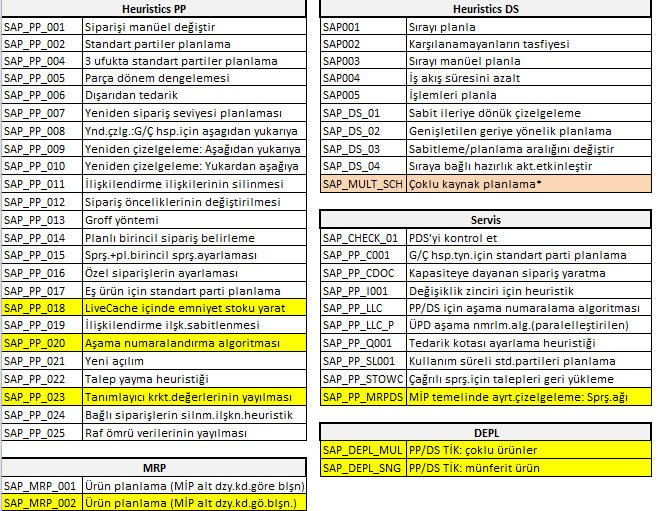
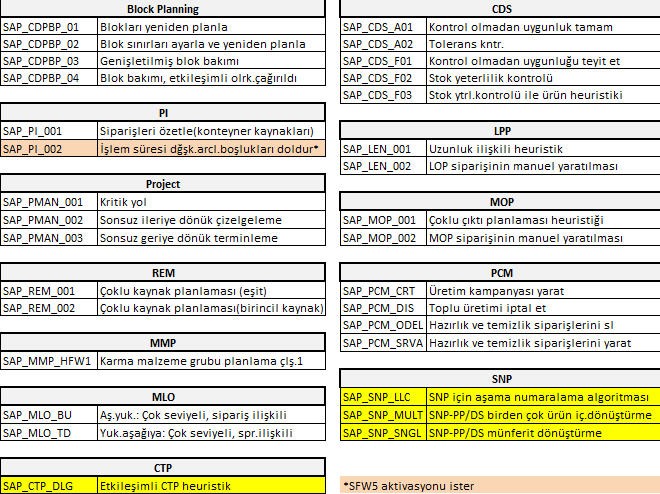
Continuous-Input/Output
Üretimde veya tüketimde kullanılabilirlik tarihi veya ihtiyaç tarihine göre belirlenen miktarları zamanda sürekli (sabit olmayan) olarak çizelgelemesini sağlamak için kullanılır. Dahili üretimde planlı bir siparişin veya bir üretim siparişinin miktarlarını kısmi miktarlara bölünmesini sağlar. Tüketim kısmında da benzer şekilde çalışır. Bu şekilde zaman ve üretilen/tüketilen miktar arasındaki ilişki kurulur.
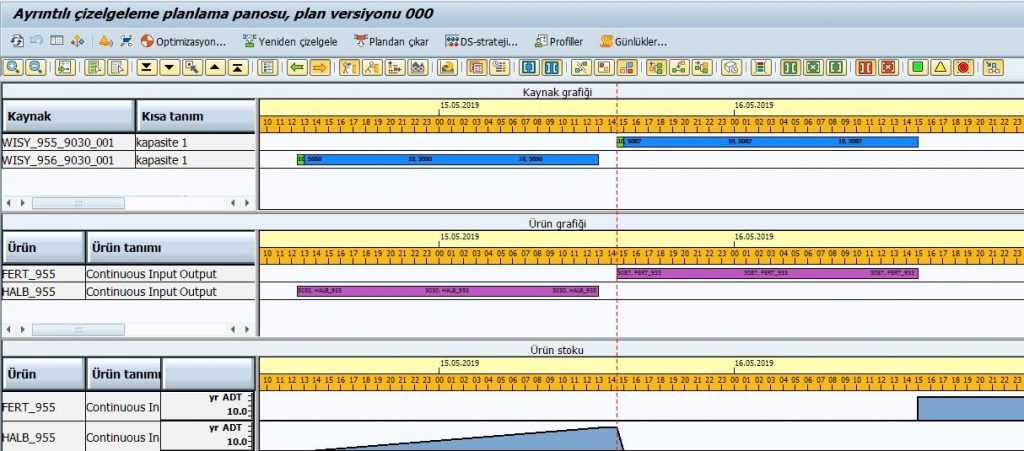
Safety Stock
Üretim Planlama ve Ayrıntılı Çizelgeleme’de (PP/DS) planlama sırasında emniyet stoğu ve hedef stok seviyelerini dikkate alabilirsiniz. Emniyet stokları, öngörülen hatalar, üretimdeki ıskartalar veya ihtiyaçlardaki mevsimsel dalgalanmalar nedeniyle öngörülemeyen ihtiyaçları dengelemek için tasarlanmıştır. Emniyet stoğunun PP/DS’de dikkate alınması için Model/Plan versiyon yönetiminde (/SAPAPO/MVM) PP/DS bölümünde ‘Emniyet stokunu dikkate al’ parametresi 2 veya 3 seçilmelidir.
0 – Emniyet stokunu dikkate alma!: Bu seçenekte PP/DS emniyet stokunu dikkate almaz. Aynı zamanda, emniyet stoğu uyarıları belirlenmez.
2 – Sanal emniyet stoku öğelerini dikkate al: Bu seçenekte PP/DS’de statik ve dinamik emniyet stoğu yöntemleri ile çalışabilirsiniz. Bir ürün lokasyon emniyet stoğu, PP/DS’nin yalnızca net ihtiyaç hesaplaması sırasında dikkate aldığı, ancak liveCache’de sipariş olarak bulunmayan sanal emniyet stok öğeleri (emniyet stok ihtiyacı veya emniyet stok girişi) ile temsil edilir.
3 – liveCache içinde emniyet mevcudu ihtiyaçlarını dikkate alma!: Bu seçeneği yalnızca sabit ve statik emniyet stok yöntemleri (SB ve SM) için kullanabilirsiniz. Sezgisel bir yöntem (heuristik) kullanarak, (/SAPAPO/HEU_PLAN_SAFETY_STOCK Emniyet Stoğu İhtiyaçları algoritmasına dayanarak) SAP liveCache’de emniyet stoğu ihtiyaçları yaratırsınız.
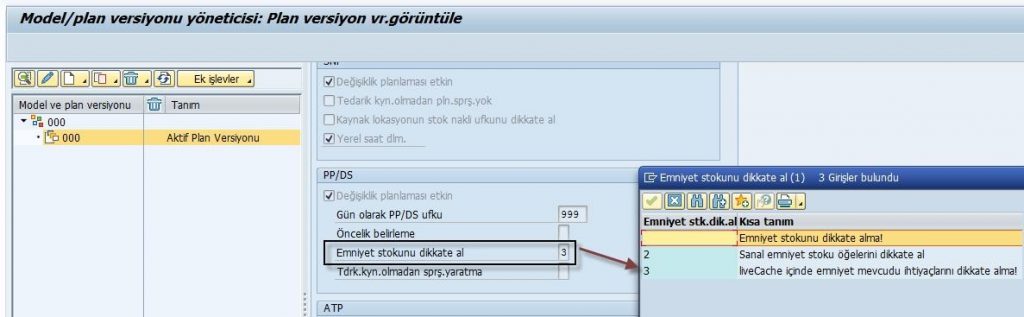
MRP Based Detailed Scheduling
SAP PP (Üretim Planlama) ‘da MRP (Malzeme ihtiyaç planlaması) ve CRP (Kapasite ihtiyaç planlaması) ayrı ayrı çalışmaktadır. PP/DS ile MRP ve CRP, kendi kapasite seviyelendirme kurallarınızı kullanarak aynı anda çalıştırılabilir. Böylece, PP/DS üretim planlama sonuçlarında daha iyi bir doğruluk sağlar.
Üretim planlama çalışması, ihtiyaçları ve kapasite planlama işlevlerini yerine getirmek için çok yönlü ve esnek bir platformdur. Özellikle, önceden oluşturulmuş ve parametreleri belirli olan varyantlar kullanılarak tamamen otomatik hale getirilebilir. Bir malzeme ihtiyaç planlamasının ve kapasite planlamasının ardışık yürütülmesi (örneğin, bir üretim planlama çalışması sırasında) hem mümkündür hem de tavsiye edilir. Bu durumda, malzeme ihtiyaç planlaması yöntemi, ihtiyaçları karşılamak için ve kaynak durumunu dikkate almadan (sonsuz) kullanılır. Sonuçta ortaya çıkan kapasite ihtiyaçları, ilgili kaynakların mevcut kapasitesi ile karşılaştırılacaktır. Bu konsept şeffaf ve yüksek kaliteli sonuçlar sağlar.
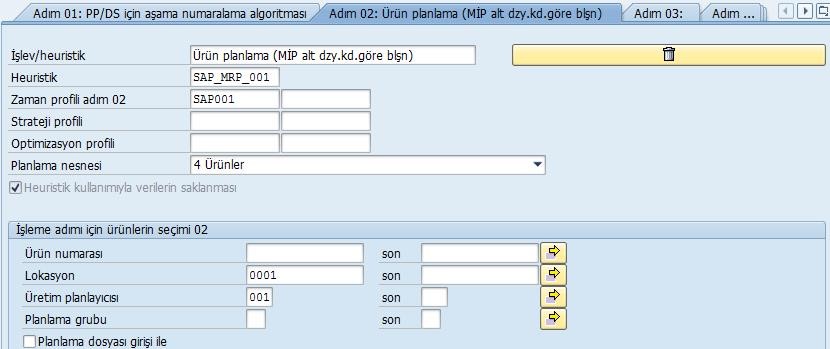
Planning Procedure
Planlama prosedürü bir ürünün nasıl planlanacağını belirler. Planlama prosedürünü tanımlarken, ‘Olay’ ve bu olayı izlemesi gereken ‘İşlem’ belirlersiniz. Olay içerikleri olarak: Bir satış siparişini yaratma ve değiştirme, yeni bir ikincil ihtiyaçlar oluşturma veya ürün ana verisini değiştirme gibi. İşlemler ise: Planlama Dosyası Girişi Oluştur, Hemen Ürün Heuristik Başlamayı vb. içerebilir. Bir ürün için uygulanması gereken eylemlerin çok hassas bir şekilde belirlenmesi için bu ayarları kullanabilirsiniz. Hemen planlama, planlama sonuçlarının olumsuz bir şekilde etkilenmemesi için kesinlikle gerekli olan olaylarla sınırlı olmalıdır.
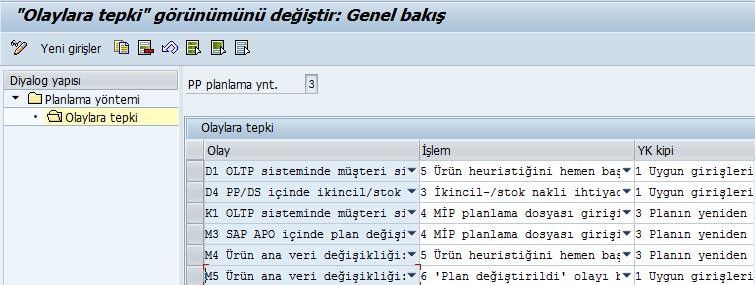
Net Requirements Calculation
Sistem, bir ürün-lokasyonun tedarik planlaması sırasında net ihtiyaç hesaplamasını kullanır. Bunu yapmak için, sistem ürün stoğu, ihtiyaçları ve giriş öğelerini dikkate alır. Net ihtiyaç hesaplaması, sistemin bir ürün için tedarik planlaması sırasında gerçekleştirdiği ilk adımdır. Açık miktarları karşılamak için, sistem net ihtiyaç hesaplamasından sonra tedarik öğeleri yaratmaya çalışır.
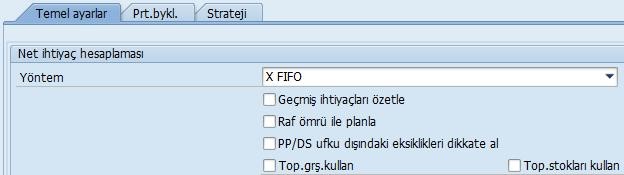
Yöntem olarak:
• FIFO Prosedürü: FIFO prosedüründe (FIFO = ilk önce ilk çıktığında) sistem, sabit giriş öğelerini kronolojik sırayla tüketir.
• Fazlalıklardan Kaçının: Bu prosedür, mümkün olduğunca az fazlalık üreten bir dengeleme mantığı kullanır.
• Gecikmelerden Kaçının: Bu prosedür mümkün olduğunca az gecikme üreten bir dengeleme mantığı kullanır.
Setup Matrix
Bir üretim sürecinde siparişlerinin sırası planlanırken siparişler arasındaki geçişte kayıpların ortaya çıktığı zamanlar vardır. Malzemelerdeki değişiklikler, üretim arasındaki temizlik, makinalarda takım değişiklikleri vb. durumlar bu kayıplara örnek olabilir. Harcanan bu zamana “hazırlık süresi” veya “geçiş süresi” denir. Geçiş sürelerini azaltarak, üretimde verimliliği ve dolayısıyla üretkenliği artırabilirsiniz. Bu geçiş sürelerini PP/DS’de oluşturma yöntemi setup matrisleridir.
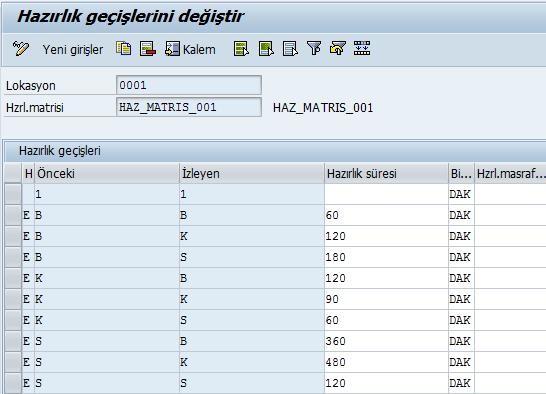
Optimizasyon çözüm sırasında belirlenen matrisi dikkate alarak hazırlık süresi/maliyetini minimize etmeye çalışmaktadır.
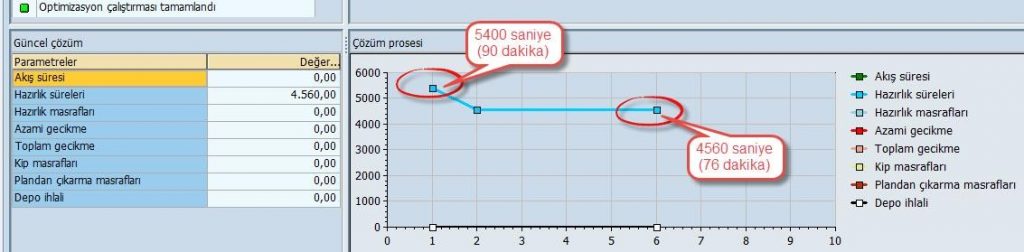
Generated Setup Matrix
Ambalaj malzemeleri üreten bir organizasyonda yükseklik ve boyut gibi değerler farklı kurulum sürelerinin ortaya çıkmasına neden olabilir. Karakteristik olarak yönetilecek bu tür değişkenler kullanılarak hazırlık grubu veya hazırlık grubu anahtarlarının bakımı kolaylıkla yapılabilmektedir.
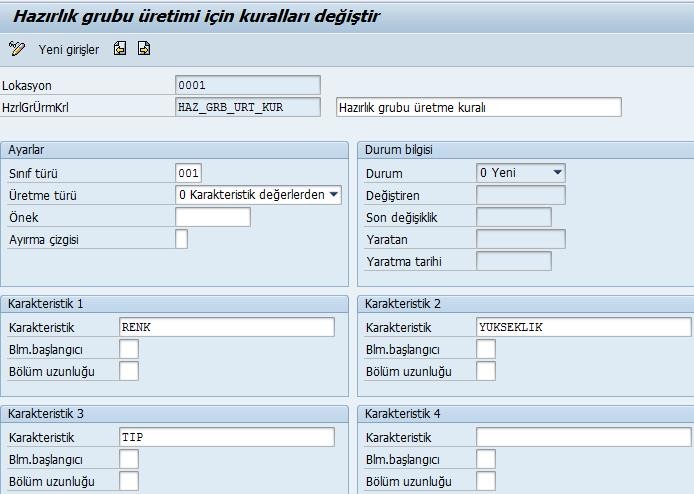
Pegging (Dynamic, Fixed)
Girdi-çıktı ilişkilendirmesi, bir ürün lokasyon üzerindeki tedarik öğeleri ile ihtiyaç öğeleri arasında mantıksal bir ilişki oluşturan bağlantıyı içerir. Sistem, tedarik öğelerine ihtiyaç öğelerini tayin etmek için bu ilişkileri kullanır. Bağlantılar daima, ürün, lokasyon ve hesap atamasının (stokta veya siparişe göre düzenlenmiş vb.) karşılıklı olarak eşleştiği bir eşleme alanı içindeki kullanılabilirlik ve talep tarihlerinden kaynaklanır.
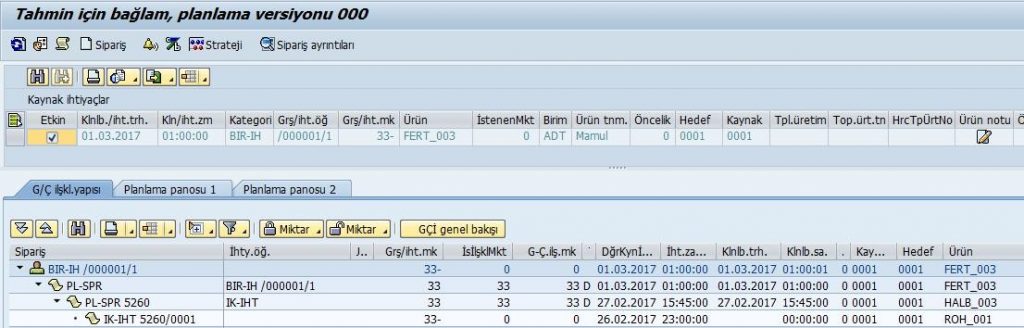
Girdi-çıktı ilişkileri, planlı birincil ihtiyaçlara atanmış planlı siparişlere, bunların ikincil ihtiyaçlarına ve hatta tüm ürün ağacı yapısına kadar uzanabilir. İlişkilerin toplamına bir (çok seviyeli) girdi-çıktı ilişkisi ağı denir. Bir siparişin girdi-çıktı ilişkisi ağını ürün görünümünden siparişin ‘Bağlam’ raporunu kullanarak görüntüleyebilirsiniz.
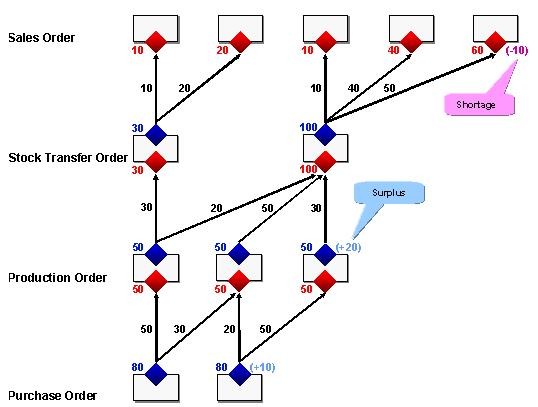
Alert Monitor
PP/DS planlama sürecinde istisnai, beklenmedik veya kritik durumları göstermesini istediğiniz uyarıları tanımlayabilirsiniz. Uygulamanızın sorunsuz çalışıp çalışmadığını izlemek için Uyarı İzleyicisi’ni kullanabilirsiniz. Bunu yapmak için sistemin sorunu hangi durumlarda bildirdiğini, diğer bir deyişle bir uyarı oluşturduğunu belirtmek için uyarı profilleri kullanırsınız. Uyarı İzleme penceresinde, meydana gelen tüm uyarıları izleyebilir ve sorunu çözmek için doğrudan ilgili uygulama işlevine gidebilirsiniz.
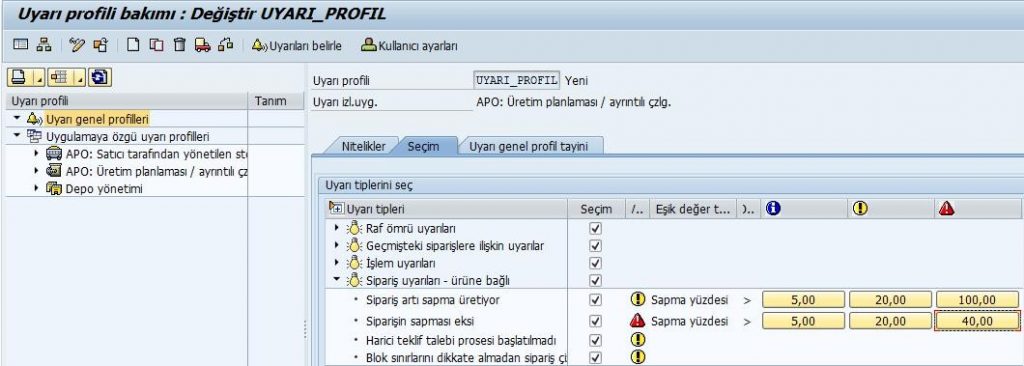
Uyarı izleme, istisna mesajları merkezi olarak yönetmek ve değerlendirmek için planlama sırasında kullanabileceğiniz bir araçtır. Bu nedenle, PP/DS planlaması bağlamında ortaya çıkan istisnaları göz önünde bulundurabilir. Sorunlar hakkındaki mesajlar, uygulamadan Uyarı Monitörüne otomatik olarak aktarılır. Her istisna mesajı belirli bir sorun durumuyla ilgilidir.
Uyarı izleyicisinin öncelikli görevi, istisna mesajları yapılandırılmış bir şekilde listelemektir. Mesajlar tanımlanmış seçim kriterlerine karşılık gelir. Uyarı monitörü, istisna mesajları kullanarak sorun hakkında genel bilgi verebilir.
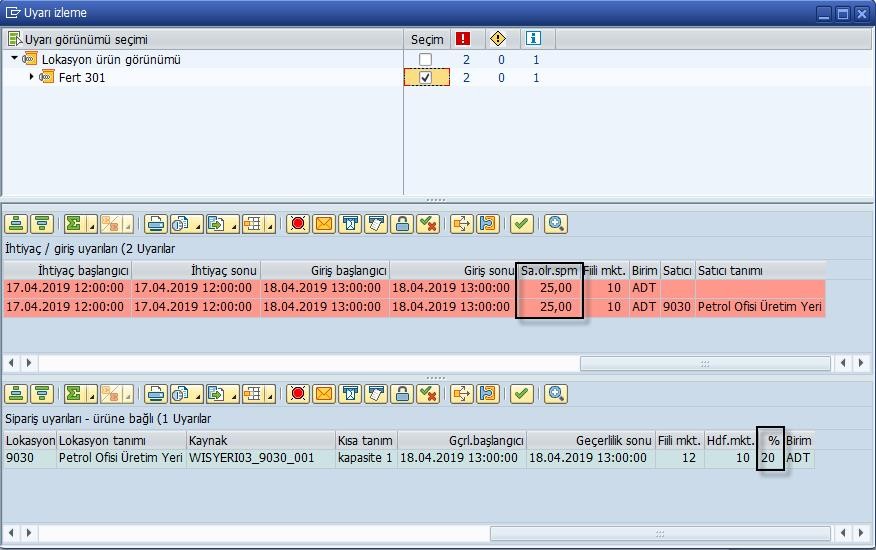
SAP_MULT_SCH – Multiresource Planning
Proses endüstrisi senaryolarında kullanılmak üzere sezgisel SAP_MULT_SCH (İşlev modülü /SAPAPO/HEU_MULTIRES_SCHED) bulunmaktadır. Tedarik önerilerini istenen tarihe kadar yakın tutmak için tanımlanmış zaman bloklarına göre tedarik kaynaklarını değiştirmek için bu algoritmayı kullanabilirsiniz.
ERP sisteminde tanımlanan üretim versiyonları PP/DS’te üretim verileri yapısı (PDS) olarak aktarılmaktadır. Birden çok üretim versiyonu olması durumunda her üretim versiyonu birer alternatifliği temsil eder. Benzer şekilde PP/DS’de üretim verileri yapıları bu alternatifliklerin yönetilmesini sağlamaktadır. Sipariş çizelgelenmesi sırasında bu alternatifler dikkate alınarak planlama yapılabilmesi için SAP_MULT_SCH heuristiği kullanılır.
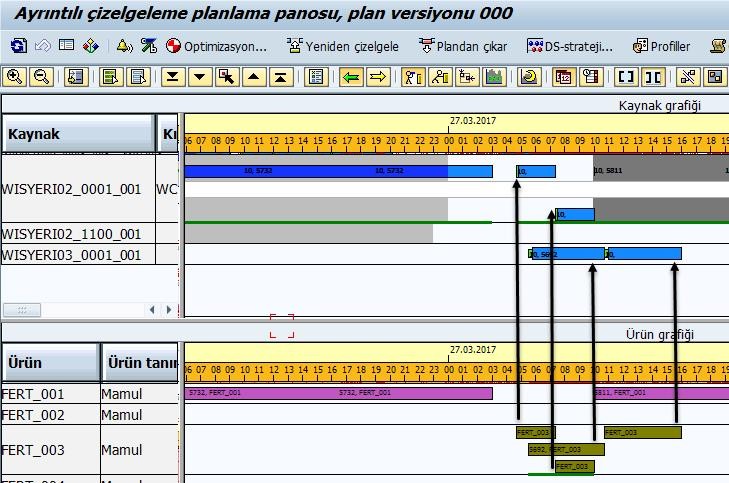
External Relationship
PP/DS’in veri modeli siparişler arası ilişkilere izin verir. Dış ilişkiler farklı siparişlerin faaliyetlerini birbirine bağlar. İç ilişkiler gibi, siparişler arası ilişkiler de minimum ve maksimum aralıkları tanımlamanıza izin verir. Bir “son-başlangıç ilişkisi” hiyerarşi yapısı sahip olan bir A1 aktivitesi ile A2 aktivitesi arasındaki bir dış ilişki, A1 aktivitesinin her zaman A2’den önce gerçekleştirileceğini belirler. Bu tür dış ilişkiler PP/DS optimizasyonu tarafından dikkate alınır.
GR Processing Time / GI
Bir ürünün teslimi veya üretimi ile stok olarak bulunabilirliği arasındaki süredir. Bu süre, örneğin kalite kontrolleri için kullanım süresi olarak kullanılır, nakliye süresine veya bir ürünün üretim süresine eklenir. Planlı bir sipariş oluştururken, sisteme planlama sırasında mal giriş işlem süresini hesaba katmasını sağlayabilirsiniz. Mal girişi işlem süresi, son satırdaki aktivitenin bitiş zamanına eklenir. Bu daha sonra planlanan siparişin bitiş zamanını (kullanılabilirlik tarihini) verir. Bu değeri ondalık noktaları da kullanabilirsiniz – örneğin 0,08 gün.
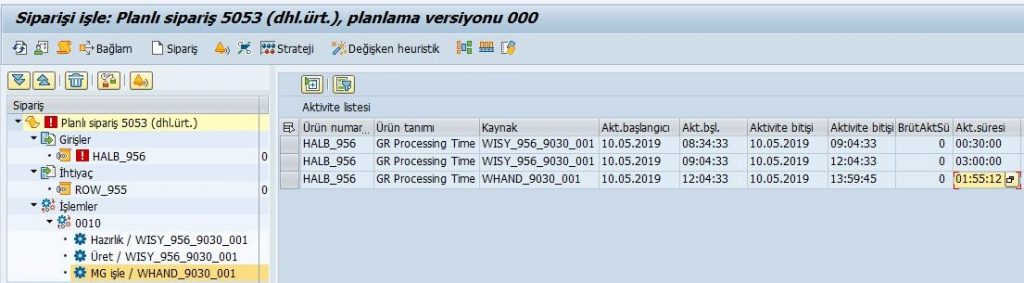
DS Scheduling Mode, Strategy Parameters
Ayrıntılı çizelgeleme, çeşitli planlama koşullarını (örneğin kaynak kullanılabilirliği gibi) dikkate alarak, kaynaklarda sipariş veya işlemlerin planlanmasını sağlar. Ayrıntılı çizelgeleme ile:
· Operasyonların gerçekleştirilmesi, kaynak ve ürün kullanılabilirliğinin dikkate alınması için kaynakları ve tarihleri / saatleri belirleyin
· Kaynak üzerindeki işlemler için en uygun işlem sırasını oluştururken destekleyin
Temel detaylı çizelgeleme faaliyetleri:
· Yeniden planlama, önceden çizelgelenmiş işlemleri farklı bir tarih / saate veya farklı kaynaklara gönderme
· Plandan çıkarma, yani çizelgelenmiş işlemleri kaynak programından kaldırma
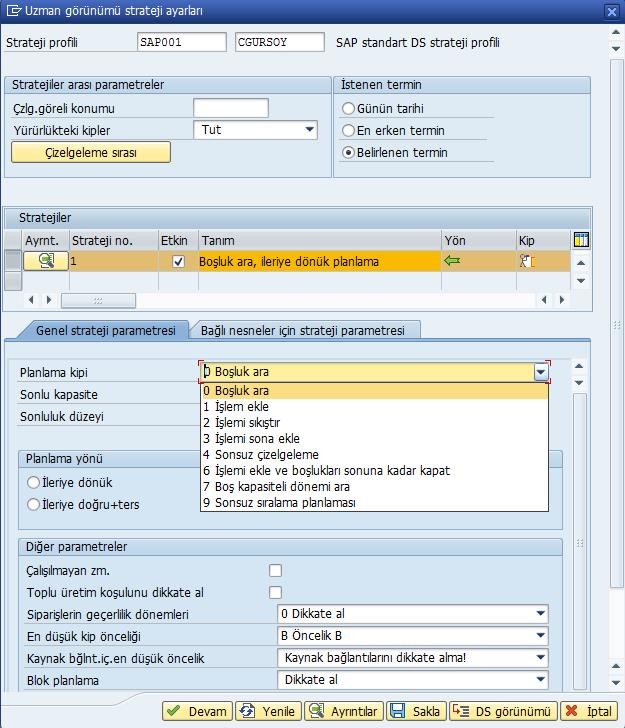
Secondary Resource
İşyerlerinin aynı ikincil kaynak üzerine kapasite ihtiyacı düşürebilmesi için yeni bir kapasite tanımlaması yapılır. Burada genellikle iki veya daha fazla kaynağın aynı anda çalışamaması durumları yönetilir. Aynı anda çalışamayacak kaynaklara tanımlanan ikincil kaynak atanarak kapasite kısıtlaması sağlanır. İkincil kaynak üzerindeki münferit kapasite sayısı herhangi bir zamanda çizelgelenebilecek akvitite miktarını temsil etmektedir.
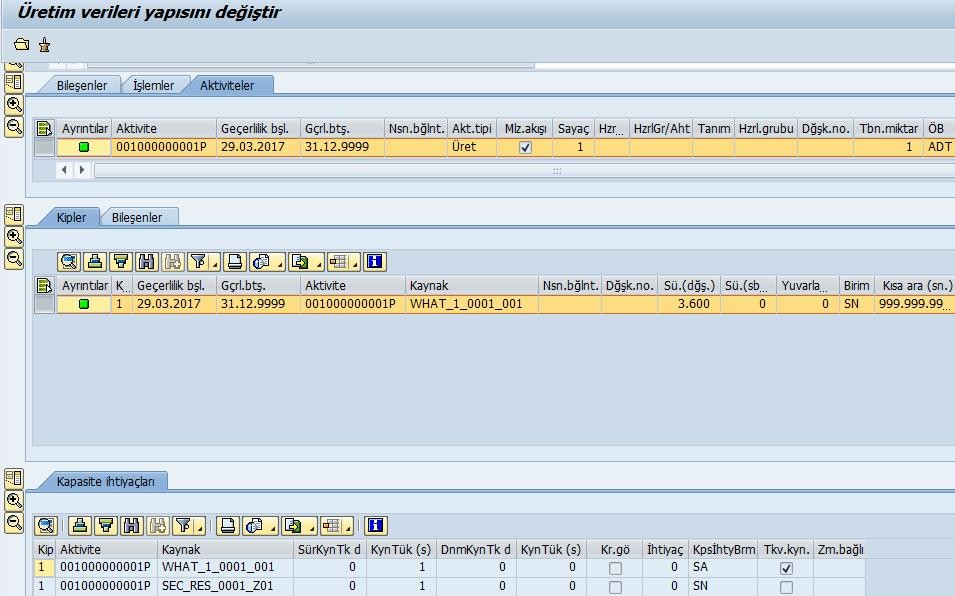
Üretim versiyonlarının üretim verileri yapısı (PDS) olarak aktarımının ardından aktiviteler içerisindeki kipte bulunan kapasite ihtiyaçları hem işyerinin birincil kaynağı için hem de ikincil kaynağı için oluşur.
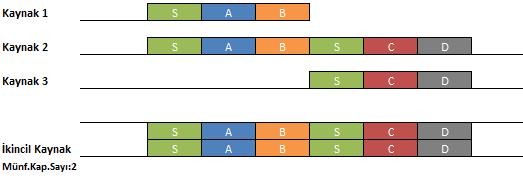
Days’ Supply, Safety and Target Stock Level
Ürün miktar açığından veya yüksek stok seviyelerinden kaçınmak için stokların ve girişlerin ihtiyaçlarınızı karşıladığı süreyi belirlemek için stok yeterliliği hesaplamasını kullanırsınız. Ek olarak, sistem stok yeterlilik günlerini hesaplarken giriş stok yeterliliğini de dikkate almaktadır.
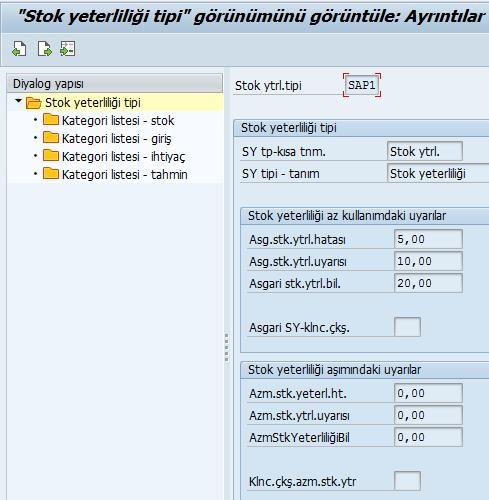
Characteristic Dependent Planning & Block Planning
Değişkenlik içeren ürünlerde için dahili üretimi planlamak için karakteristik bazlı planlama (CDP) kullanabilirsiniz. Bu ürünler için planlı siparişleri ve üretim siparişlerini PP/DS tarafında yapılandırabilirsiniz. CDP’nin en çok uygulanan özelliği olan Blok planlamada, işlemlerin planlanacağı blokları bir kaynaktaki belirli karakteristik değerlerle tanımlarsınız. Siparişler, karakteristik değer atamalarına bağlı olarak planlanır. Blok Planlama, kapasiteleri daha rasyonel kullanmak amacıyla, belirli özelliklere sahip ürünler için kaynak kapasitelerinin planlanması veya önceden atanmasıdır. Nitelikler, SAP sistemindeki karakteristikler kullanılarak tanımlanmıştır. Blok planlamada, belirli bir süreye ve özniteliğe sahip bir kaynakta, örneğin üzerinde çeşitli renklerde ürün ürettiğiniz blok başına belirli bir süreyi tanımlarsınız. Karakteristik bazlı planlama (CDP) belirli ürünlerin özelliklerini kullanarak planlanmaktadır. Bu özellik sayesinde, giriş öğeleri aynı karakteristik değerlere dayanan ihtiyaçlarla eşleştirilir.
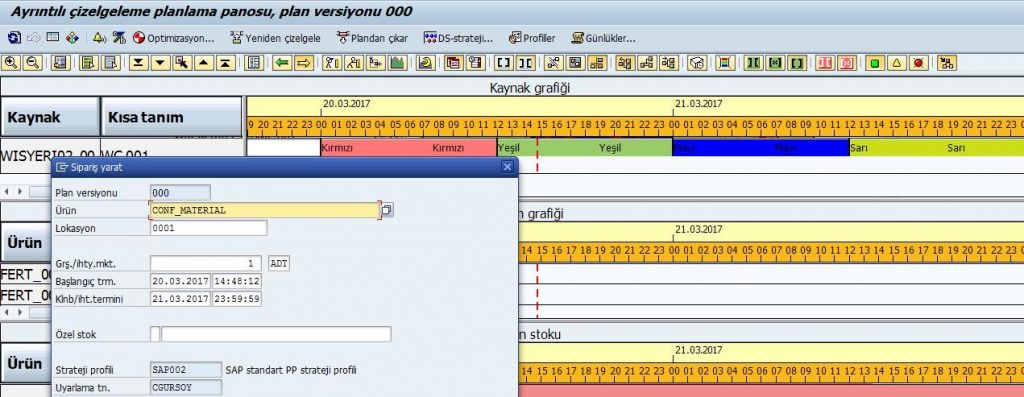
Interchangeability in PP/DS
Ürünlerin sürekli gelişimi veya üretim süreçlerinde yapılan değişiklikler, bir ürün yerine ve başka bir ürünle değiştirmeyi gerekli kılabilir. PP/DS, ikame ilişkileri doğrusal bir üst zincir ile temsil edilen değiştirilebilir ürünler için tedarik planlama ve sipariş işlemeyi destekler. Doğrusal bir üst zincir, farklı ürünlerin birbirinin yerine geçmesi ile sağlanır. Ürün veya ürün-lokasyon için değiştirebilirlik tanımlaması sonucu planlama ve/veya ATP bazında sağlanabilmektedir.
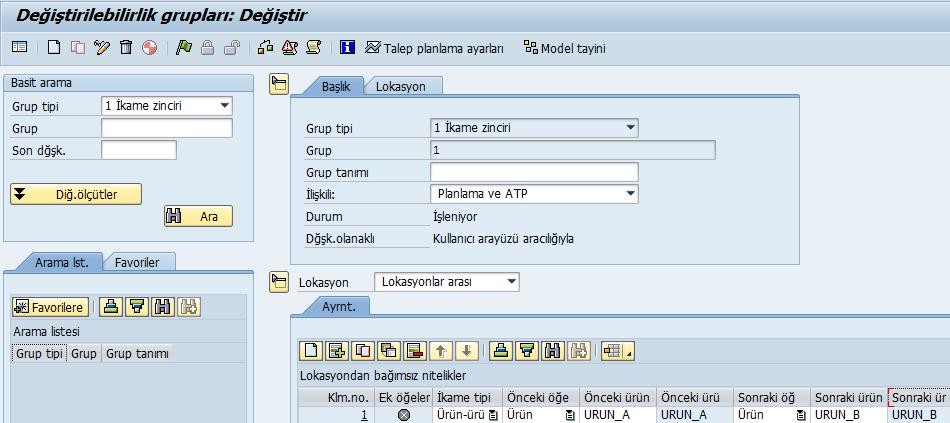
Campaign Planning
Proses endüstrilerinde ağırlıklı olarak üretim hatlarında sıralanacak ürünler için toplu üretim kullanılmaktadır. Bu üretim hatları, farklı ürenlerin işlenmesi için ya hazırlık yapmalı ya da temizlenmelidir. Toplu üretim planlamasının asıl amacı, hazırlık maliyetlerini ve depolama maliyetlerini azaltmaktır. Örneğin, üretim hattında sık sık yapılan değişiklikler depolama maliyetlerini düşürmeye yardımcı olabilir ancak aynı zamanda hazırlık maliyetlerinde artışa neden olabilir. Öte yandan, üretim hattı mümkün olduğunca nadir olarak kuruluyorsa, bu durum hazırlık maliyetlerini düşürebilir, ancak aynı zamanda depolama maliyetlerini de artırabilir. Özellikle hazırlık ve depolama maliyetlerini düşürmek için aynı veya benzer ürünleri üreten siparişleri bir üretim numarası altında birleştirmek için toplu üretim planlama işlevlerini kullanabilirsiniz.
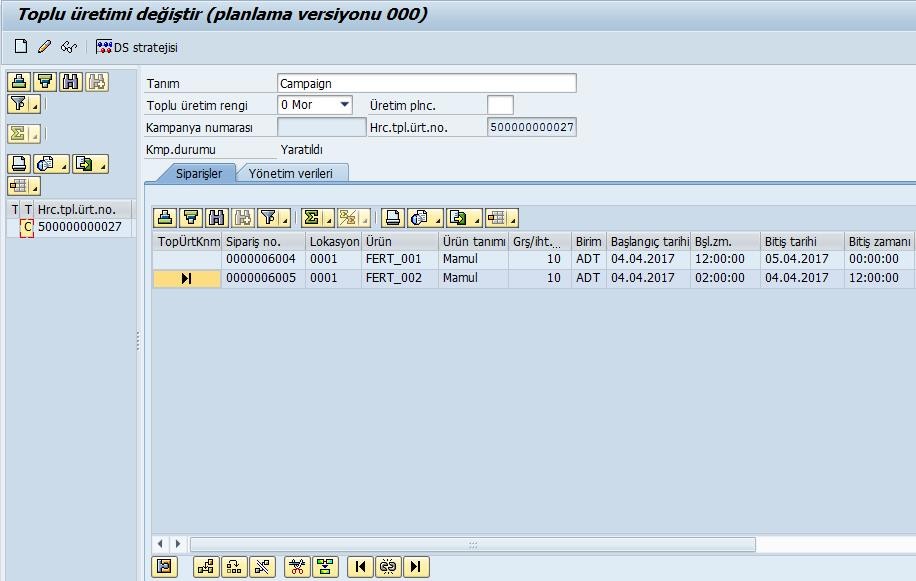
Push Production
İtmeye dayalı üretimi, kısa vadeli ila orta vadeli planlamada bir itme problemini (malzemeye ihtiyaç olmadan) çözmek için karar vermeyi destekler ve üretim planı oluşturmak için kullanılır. İhtiyaç olarak ters yönde çalışan, bir itici malzemeyi tüketmek için neyin üretileceği ve hangi miktarda üretileceğine karar verilmesine yardımcı olur. Böylece, belirli bir hammadde veya yarımamul malzemesi için girdileri kullanarak üst ürünlerin planlaması sağlanabilmektedir.
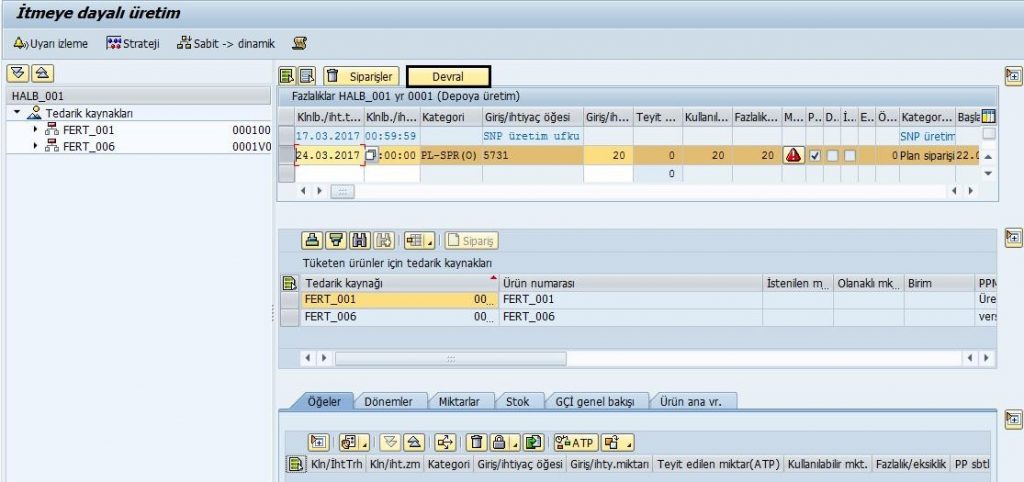
Bucket Capacity
PP/DS dönem kapasitesini sadece bir gün veya vardiya gibi belirli bir süre içinde bir sipariş için yeterli kapasitenin bulunup bulunmadığını bulmak için dönem bazlı bir kapasite kontrolü için kullanılır. Döneme yönelik kapasite kontrolünü CTP işleminde ve blok planlamada kullanabilirsiniz.
Capacity Reservation
Kaynak üzerinde dönem kapasitesi görünümünde dönem tanımı alanını ‘Blok planlamadan’ olarak seçerseniz, sistem, blok planlaması için tanımladığınız bloklardan kaynak rezervasyon şemasının tanımlanmasını istemektedir. Böylece, tanımlayıcı karakteristikler aracılııyla (örneğin müşteri numarası) kapasitenin rezervasyonu sağlanabilmektedir.
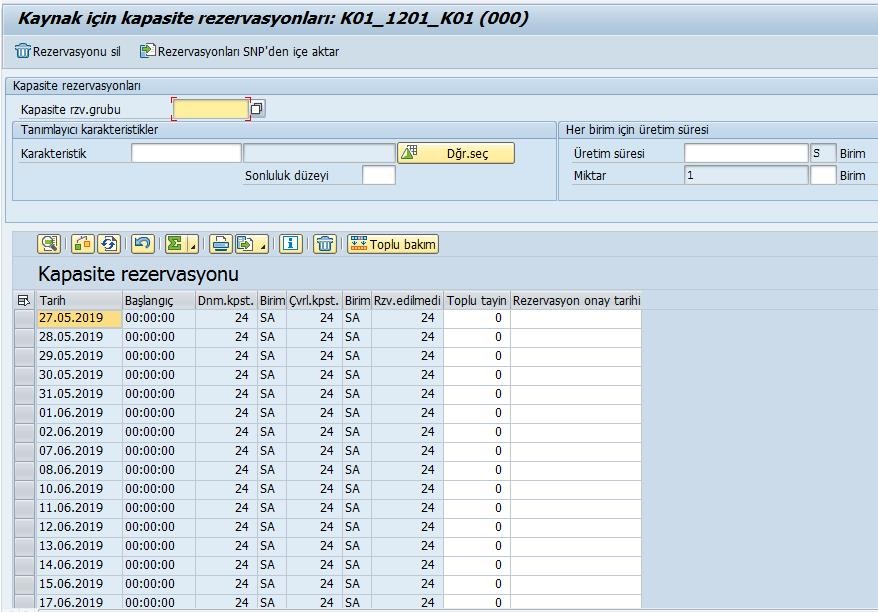
Storage Resource, Tank Planning, Container Resources
Bir konteyner kaynağı, bir ürünün depolanabileceği bir kaynaktır; depolama özelliklerine sahip çok kaynaklı bir kaynak olabilir. Böyle bir kaynak sadece zamanla değil aynı zamanda kapasite ile de sınırlıdır (hacim, ağırlık veya diğer parametreler ile tanımlanır).
Farklı ürünlerin ara depolaması için bir konteyner kaynağı üretimde kullanılabilir. Bununla birlikte, ilgili depo alanı yalnızca belirli bir zamanda sadece bir ürün içerebilir. Veya aynı anda birçok bileşen doldurabilir veya ürünleri boşaltabilir. Bunun gibi birçok durum göz önüne alıdğında ve planlama açısından konteyner, belirli bir ürün miktarı ile belirli bir süre dolan bir kaynaktır. Üretim kapasitesinin yanı sıra konteyner kaynağı da depolama kapasitesine sahiptir. Konteyner kaynaklarının depolama özelliklerine yönelik ihlaller, uyarı monitöründe görüntülenebilir ve sınırlamalar optimizasyon tarafından dikkate alınmaktadır.
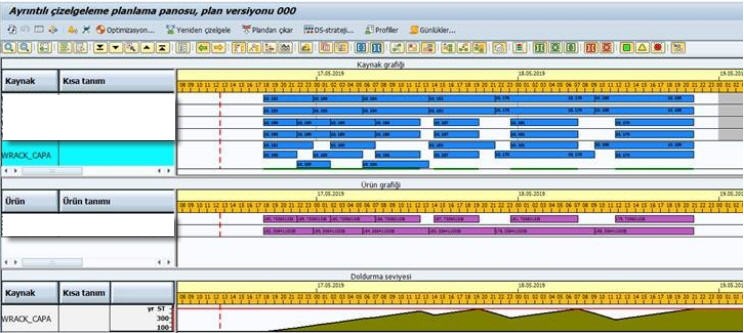
Shelf Life
Malzeme depo görünümünde yer alan raf ömrü verileri kullanılarak mevcut stok partilerinin son kullanım tarihleri veya giriş öğelerinin (planlı sipariş) son kullanım tarihlerinin planlama sırasında dikkate alınması sağlanabilmektedir.
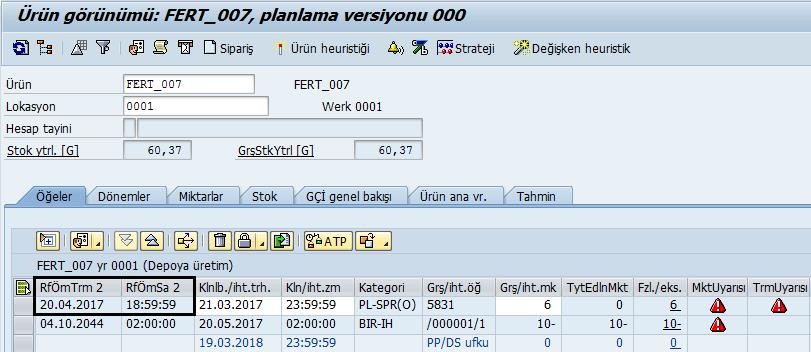
Co-Product
Eş ürün tek bir üretim sürecinde beraber üretilen ürünlerdir. Bu süreçte bir ürün ana ürün adlandırılırken diğer ürün(ler) çıktı olarak adlandırılır. Böylece, mal hareketleri eş zamanlı olarak siparişlenebilir ve takip edilebilir. Ayrıca çizelgelemede değişiklik olursa bunlar iki ürüne de birlikte yansır ve hata olasılığı düşüktür. Bu yüzden planlamada kolaylık sağlar.
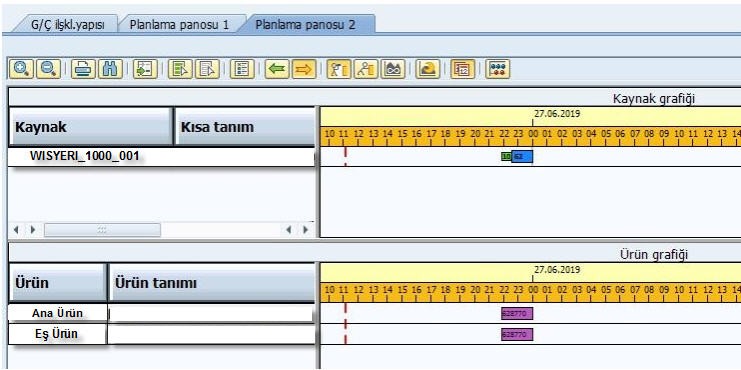
Subcontracting in PP/DS
Taşeronluk (Fason), satın alınacak ürünün, tedarikçinin bileşenleri tedarik ettiği ve nihai ürünün bir satıcı (taşeron) tarafından üretildiği bir alım şeklidir. Tedarik eden işletme bu bileşenleri taşeronlara doğrudan (tesislerinden birini kullanarak) ya da dolaylı olarak (iş ortaklarından birini kullanarak) sağlayabilir. Üretim süreci tamamlandığında, taşeron sipariş edilen ürünü malı isteyen tarafa iletir.
Resource Network
Kaynak ağları, ardışık işlemler veya siparişler için kaynak kısıtlamalarının modellenmesini kolaylaştırır. Özellikle proses endüstrileri için, bazı üretim kısıtlamalarında sıklıkla uygulanır. Örneğin, bir reaktör kaynağı üzerinde bir işlem gerçekleştirilirse, ardışık işlem için yalnızca sınırlı bir ardışık kaynak kümesi (örneğin ara malzemeler için depolama tankları veya nihai ürün veya dolum hatları) kullanılabilir.
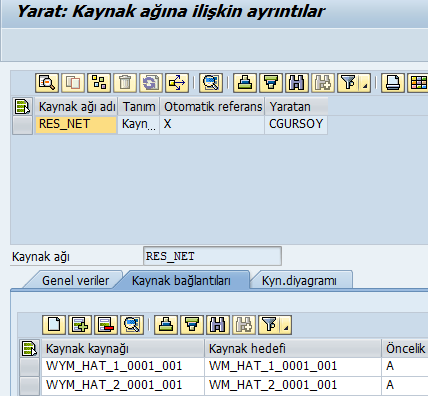
Ürün ve yarı ürün için alternatif kipler ile planlamak mümkündür. Burada ürün veya yarı ürün için alternatif bir kipe geçiş yapıldığında ilişkili olan kipler arası geçişi sağlamak için kaynak ağı kullanılmaktadır.
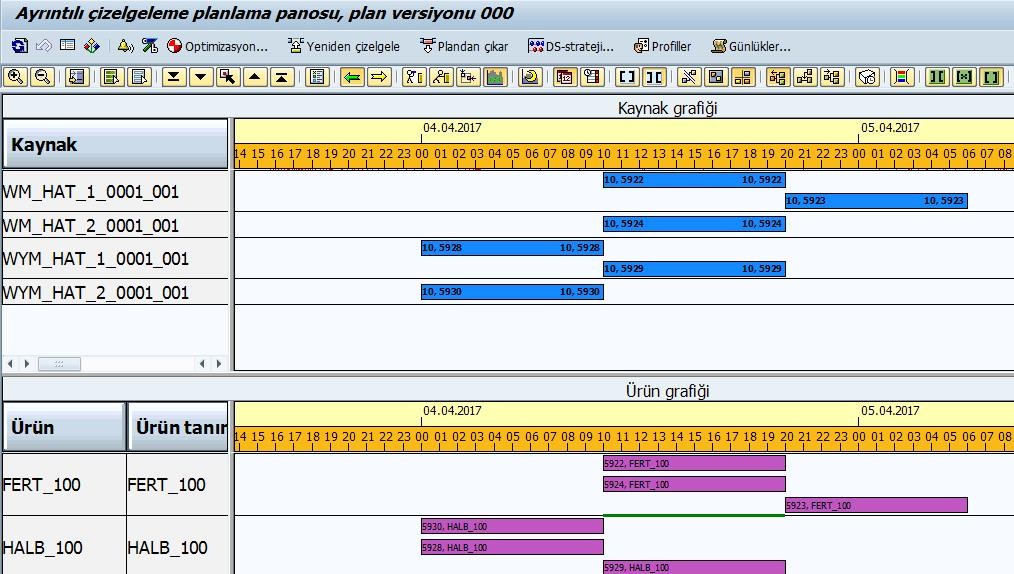
Quota Arrangements
Dahili üretim veya dışarıdan tedarikte, tedarik kaynaklarını ve bu kaynaklar arası miktar dağılımını belirlemek için kota kullanılır. ERP’dekine benzer şekilde PP/DS içinde tedarik kotasının bakımı gerçekleştirilir.
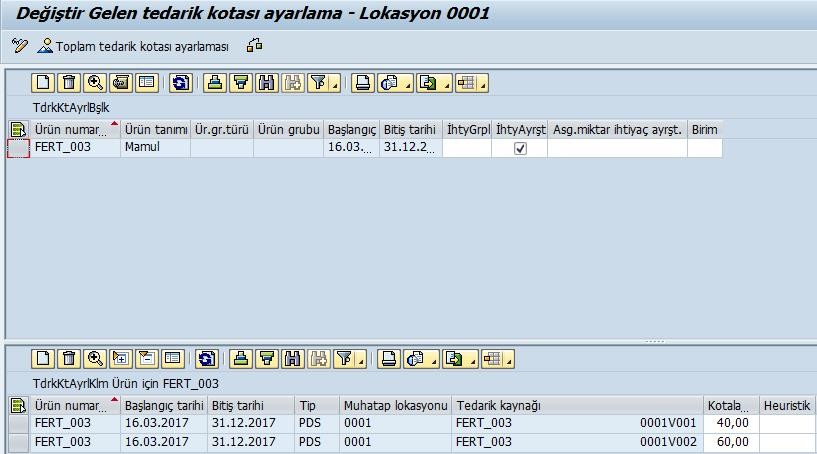
Production Scheduling Board
Ayrıntılı çizelgeleme planlama panosu, kapasite planlaması ve kapasite yük durumunun izlenmesini sağlayan grafik planlama işlevselliği sağlar. Bu bağlamla mevcut kapasite yükü, ihtiyaç tarihleri /saatleri ve hazırlık süreleri için optimize edilmiş sıralama gibi manuel veya kısmen otomatik terminleme ve ayrıca kaynaklar üzerindeki işlemlerin çizelgelenmesini içerir. Bu çalışma genellikle ayrıntılı çizelgeleme heuristik yöntemleri veya optimizasyonu gibi otomatik özelliklerle desteklenir. Gerçek dünyada kapasite planlaması çok çaba sarf edilen bir iş olduğundan yalnızca üretim sürecinde yer alan darboğaz kaynakları için ayrıntılı olarak yapılması tavsiye edilir. Kaynaklar üzerindeki faaliyetlerin, işlemlerin ve siparişlerin zaman konumunu gösteren Gantt şeması, ayrıntılı planlama planlama panosu sipariş işleme görünümünde ve ürün planlama panosuna entegre edilmiştir.
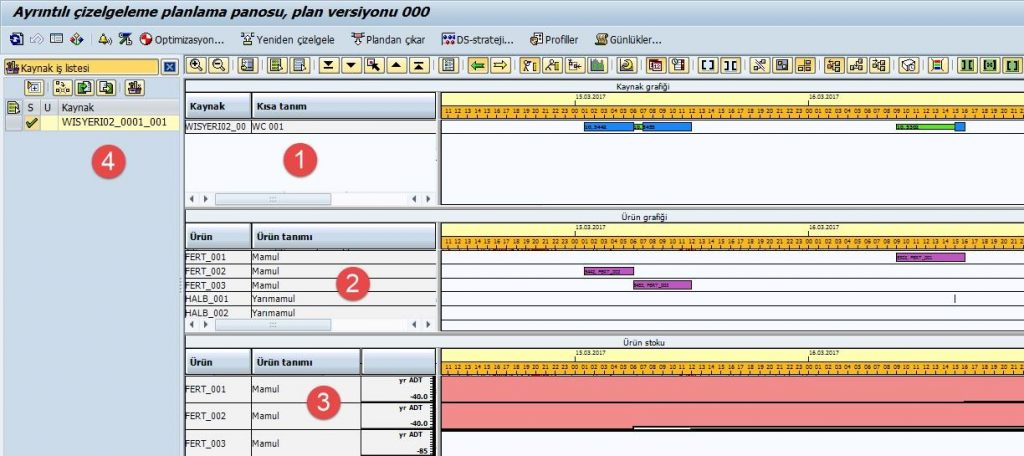
Graphical Objects on the Detailed Scheduling Planning Board
Gantt chart üzerinde bulunan aşağıdaki nesneler içerik olarak değiştirilebilir:
• Nesneler ve bu nedenle grafiğin tablo alanında görüntüleyebileceğiniz alanlar, örneğin grafik türü kaynağı (kaynak grafiği), kaynak adı ve lokasyon gibi.
• Grafiğin diyagram bölümünde görüntüleyebileceğiniz nesneler (örneğin, hazırlık veya üretim aktivitesi)
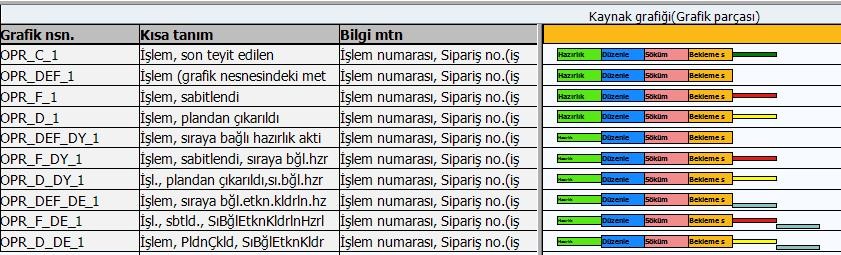
Product Planning Table
Bir ürün-lokasyonun ihtiyaçlarını / stok durumu ve üretim hatlarının durumuna genel bakış sağlar. Ürün planlama tablosu, planlama sorunlarını çeşitli açılardan netleştirmek ve işlemek için kullanabileceğiniz çok yönlü ve esnek bir araçtır. Örneğin, ihtiyaç planlamasının basit bir bakışını kullanabilir ve aynı anda ortaya çıkan kapasite durumunu değerlendirebilir, aşırı yükleri tanımlayabilir ve dinamik uyarıları analiz edebilirsiniz.
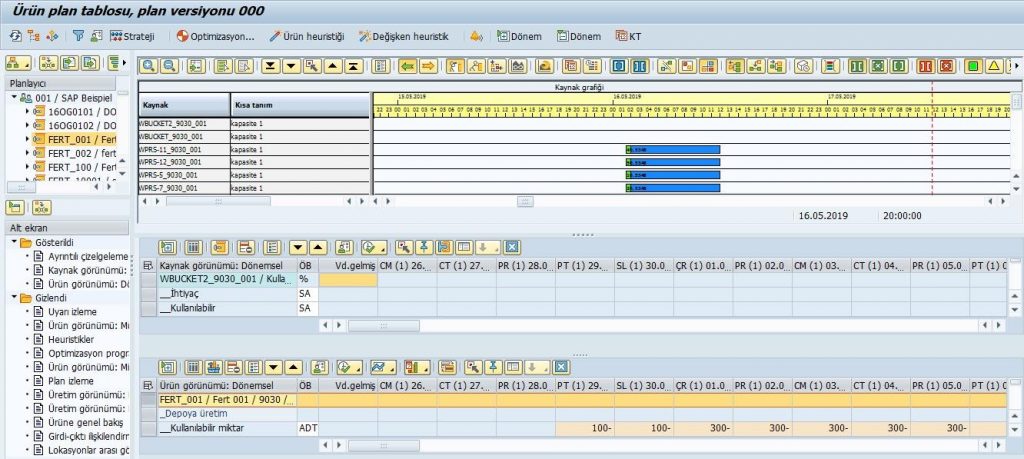
Resource Planning Table
Bir kaynağın kapasite kullanımının tablo şeklinde gösterilmesini sağlar. Kaynak planlama tablosu, ayrıntılı çizelgeleme panosuna (Gantt chart) bir alternatif sunar. Grafik bir araç olan ayrıntılı çizelgeleme panosunun aksine, kaynak planlama tablosu size kaynakların tablo şeklinde kullanımı hakkında bilgi vermektedir.
Kaynak planlama tablosu, kapasite planlaması için interaktif bir araç olarak mevcuttur. Siparişleri ve işlemleri sıralamak için tablo yönelimli bir yaklaşımla çalışırken kullanılır. Ayrıca, basitçe bir kaynakta sıralamayı ayarlama veya siparişler için çeşitli zamanlardaki (günlük, haftalık, aylık vb.) senaryolarla uğraşma konusuna gelindiğinde, grafiksel bir araçtan ziyade bir sipariş listesi içeren tablo tabanlı bir aracın kullanılması daha kolaydır. Diğer açılardan, kaynak planlama tablosunun olası kullanımı, ayrıntılı çizelgeleme planlama panosu ile benzerdir.
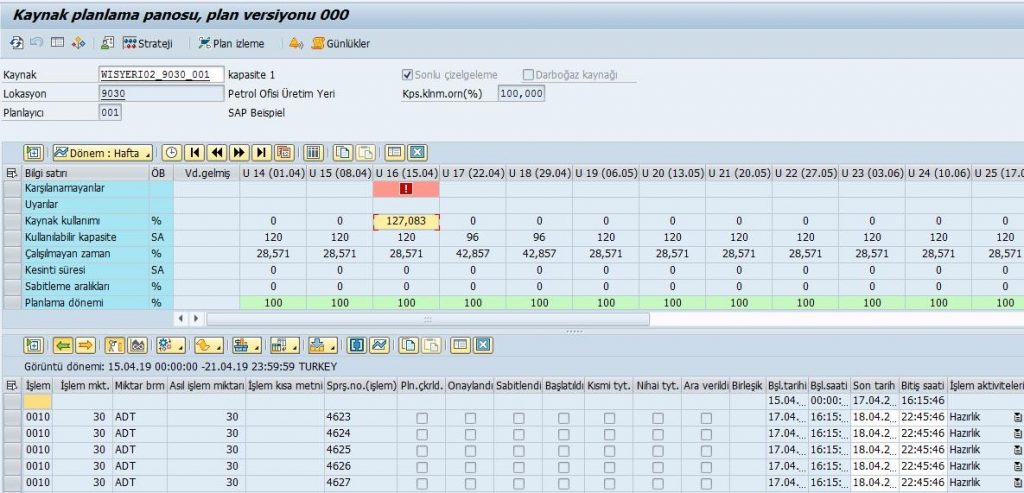
Product View
Ürün görünümü, ihtiyaç planlama için merkezi bir araçtır. Bir ürün lokasyon ihtiyaçlarına ve stok durumuna tam bir bakış sunar ve dolayısıyla ERP’deki stok/ihtiyaç listesine (işlem kodu MD04) eşdeğerdir. Ürün görünümünde girişler, ihtiyaçlar, sipariş işleme ve girdi-çıktı ilişkilerine genel bakış işlevselliğinin çoğunu içerir.
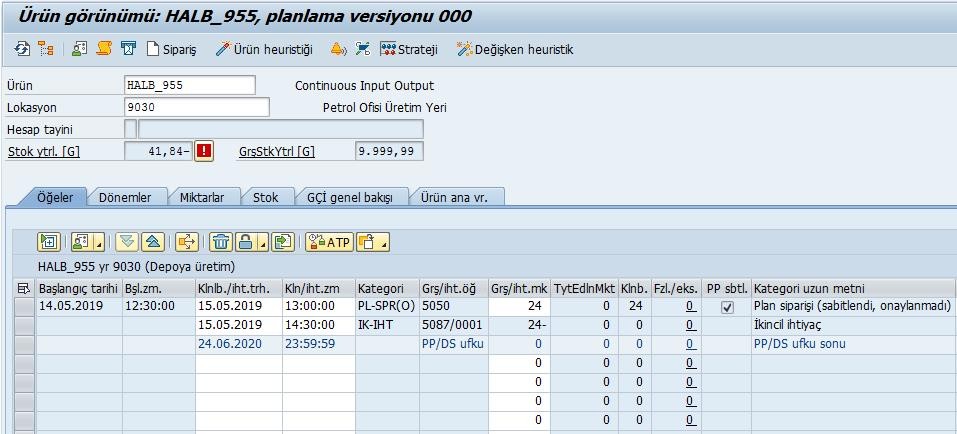
Ürün görünümü bir ürün lokasyon kombinasyonun MİP öğelerini tabloda kronolojik sırayla gösterir. Ürün görünümü, bir ürün lokasyon için geleneksel değerlendirme işlevleri sağlar. Burada bir hesap özeti gibi miktar ve tarih durumuna ilişkin girdileri okuyabilirsiniz. Giriş öğeleri ve çıkış öğeleri tarihe göre belirlenir ve her tarih için beklenen stok miktarını görebilirsiniz. Ayrıca, bir ürün lokasyonun planlama durumunu tek tek MİP öğeleri ile hedeflenen bir biçimde değiştirmek veya ilgili ürünü etkileşimli olarak bir bütün olarak planlama seçeneğiniz vardır.
Production Planning Run
Üretim planlama çalıştırmasını heuristik, ayrıntılı çizelgeleme işlevleri veya optimizasyon için çok sayıda nesne için çevrimiçi olarak veya arka plan işi olarak kullanırsınız. Üretim planlama çalışması sırasında, birbiri ardına çeşitli heuristik yöntemler veya fonksiyonlar yürütülebilir.
Üretim planlama çalışmasında esnek adımların bireysel yürütülme sırası söz konusu olduğunda, standart bir yöntem yoktur. Bir üretim planlama çalışmasıyla birlikte, operasyonel iş sürecini ayrıntılı bir şekilde tanımlama ve bunu planlama çalıştırmasının bireysel adımlarına eşleme gereksinimiyle karşılaşacaksınız. Her zaman bir kapasite planlamasından önce bir ihtiyaç planlaması yapılmalıdır. Bununla birlikte, senaryonun karmaşıklığı ve üretim planlamasının yüksek derecede esnekliği göz önüne alındığında, örneğin kendiniz için aşağıdakilere karar verebilirsiniz:
· İhtiyaç planlamasının özellikleri: (tek seviyeli, çok seviyeli). Her bir mip düzeyi için genel planlama yapılabilir mi yoksa kademeli olarak planlama gerekip gerekmediğini belirleme.
· Kapasite planlamasının özellikleri: detaylı çizegeleme heuristik, işlev veya PP/DS optimizasyonu. Klasik bir üstten alta doğru planlamanın hedeflerinize ulaşması ya da darboğaz durumundan dolayı aşağıdan yukarıya planlama yapılmasının gerekip gerekmediği.
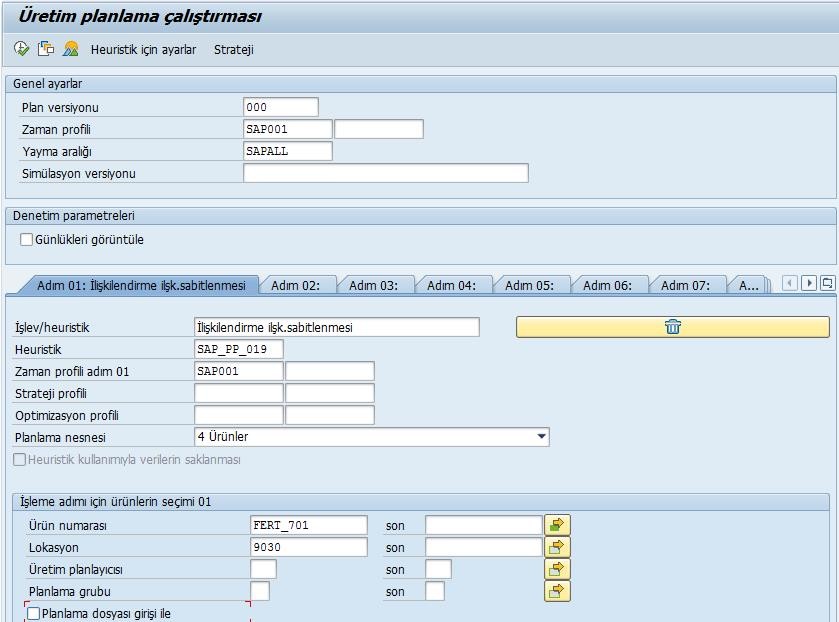
Interactive Planning & Simulation
Manuel planlama yapmak istediğiniz önemli ürünler için etkileşimli planlamayı kullanabilir veya otomatik planlama sırasında ortaya çıkan planlama problemlerini çözebilirsiniz.
Mevcut üretim kaynak yükünü belirlemek, yani kapasitenin mevcut olup olmadığını veya başka bir sipariş tarafından önceden ayrılmış olup olmadığını belirlemek için bir kontrol gerçekleştirilirse, bu sonlu çizelgeleme olarak adlandırılır. Sınırlı kapasite planlaması, genellikle tarih değişiklikleriyle sonuçlanır, çünkü darboğaz kaynakları planlanabilir olduğunda zaman boşlukları bulunmalıdır. Bir tarih öne çekilirse, siparişin kullanılabilirlik tarihi bunun sonucunda ertelenir. Öte yandan, emir daha sonraki bir zamana (geriye) taşınırsa, üretim için gerekli malzemelerin ikincil ihtiyaç tarihleri de ertelenir ve sonuçta giriş öğeleri zamanında bu ihtiyaçları karşılayamaz.
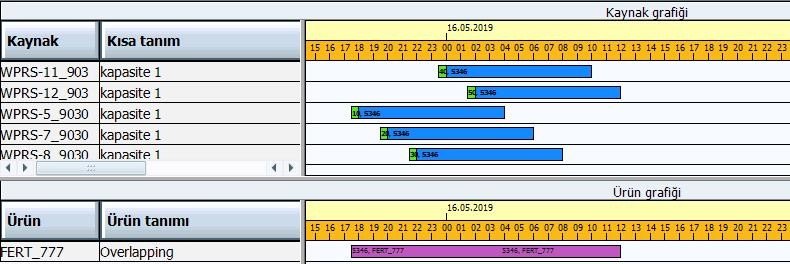
Cross-industry and industry-specific solutions
PP/DS, üretim türleri (örneğin siparişe göre üretim veya stoka göre üretim) ve üretim tiplerine (örneğin kesikli üretimi, seri üretim veya proses üretimi) özgü bir çok işlemi destekler. Standart çözümlere ek olarak, sektöre özel çözümler de mevcuttur.
Repetitive Manufacturing (REM)
Stoğa üretim stratejisini kullanarak planladığınız konfigüre edilemeyen ürünler için planlama aracı olarak PP/DS’de seri üretimi kullanabilirsiniz. Üretim yürütme ve kontrol fonksiyonlarını PP/DS’in seri üretim ekranları kullanılarak gerçekleştirilir. Ayrıca, otomotiv endüstrisinde yaygın olarak kullanılan konfigüre edilebilir ürünleri, siparişe özel üretim senaryosu ile planlayabilirsiniz.
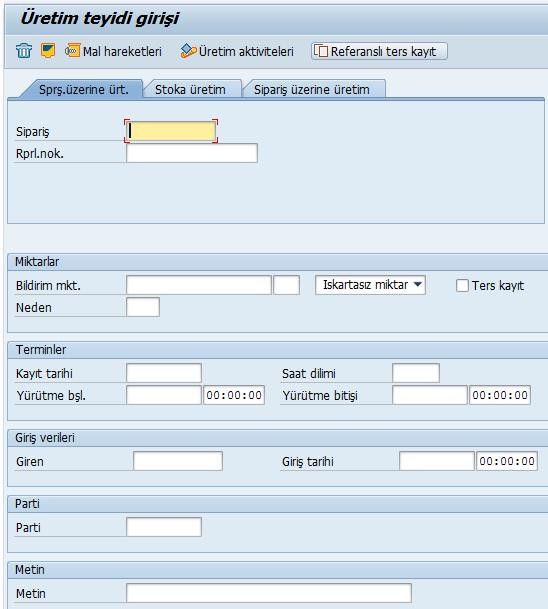
REM – Multiresource Planning
Üretim Planlama ve Detaylı Çizelgeleme (PP/DS) alanındaki belirli problemleri çözmek için sezgisel yöntemler bulunmaktadır. SAP, seri üretimde (REM) planlama için iki temel seri üretim sezgisel (heuristik) yöntem sunar.
Seri üretim sezgisel yöntemleri, çoklu hatlarda (dolum hatları gibi) üretilecek ürünleri planlamak için uygundur. Bu sezgisel yöntem ile eşzamanlı olarak birkaç kaynak (PDS) planlayabilirsiniz. Bu şekilde alternatif kaynaklar (hatlar) üzerinde ürünler üretebilir ve bunları sonlu planlamada istediğiniz gibi kaynaklar üzerine yükleyebilirsiniz.
• Çoklu kaynak planlaması (eşit) – SAP_REM_001
Bu sezgisel yöntemde, kaynaklar mümkün olduğunca eşit biçimde yüklenir.
• Çoklu kaynak planlaması (birincil kaynak) – SAP_REM_002
Bu sezgisel yöntemde, tercih edilen kaynak olarak tanımlanan kaynaklar öncelikli olarak yüklenir. Planlı siparişler, alternatif kaynaklara ancak tercih edilen kaynaklar tam kapasitede olduktan sonra taşınır.
Her iki REM sezgisel yöntem başlangıçta net ihtiyaç hesaplamasını yapar, ardından ürün parti büyüklüğündeki ayarlara göre miktarı hesaplar. Sonunda, her dönem için mevcut uygun kaynak kapasitesini göz önünde bulundurarak, mevcut ihtiyaçlar için planlı siparişleri yaratır. Heuristik ayarlarınıza bağlı olarak, periyotlar günlük, haftalık veya aylık olabilir. Kullanıcı tanımlı zaman dilimleri de mümkündür.
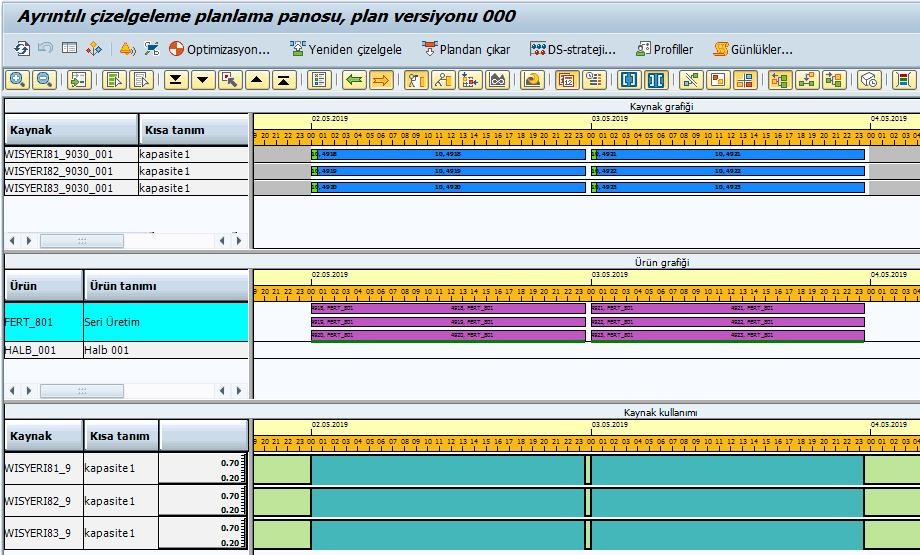
Project Manufacturing and Make-to-Order Manufacturing
Üretim Planlama ve Detaylı Çizelgelemede (PP/DS), satış siparişleri ve proje siparişleri için çok seviyeli sipariş ağları planlayabilirsiniz. Bu planlama, kritik yolun planlanması ve belirlenmesi için heuristik yöntemler ile desteklenir. Bir sipariş ağındaki kritik yolu (bir sezgisel yöntem kullanarak) analiz ederek, darboğazları tespit edebilir ve ağı uygun yerlerde azaltabilirsiniz.
Project Order
Müşteriye özel ürünler için proje üretiminin yanı sıra, yeni ürün geliştirme için de projeler kullanılmaktadır. Genellikle prototip oluşturmak için malzeme ve kapasite ihtiyaçlarını içerirler ve bu nedenle entegre proje ve malzeme planlaması gerektirir. PS’de ağ planlarını PP/DS’deki bir proje siparişine entegrasyonu, işlemleri , ilişkileri ve malzeme ihtiyaçlarını içerir. Proje sipariş gerekliliklerini PP/DS’de planlayabilirsiniz.
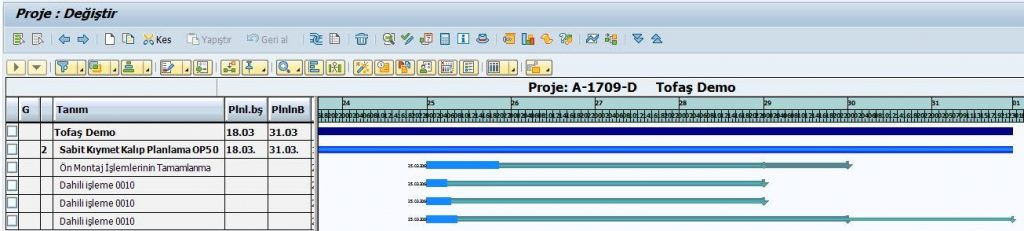
Maintenance Orders in PP/DS
Bakım onarım (PM) siparişi, teknik nesnelerde (teknik birim ve ekipmanlar gibi) bakımın planlanması, yürütülmesi ve kontrol edilmesi için kullanılır. PM siparişi bir arızadan dolayı veya önleyici bakım (planlı bakım) gerçekleştirmek için yaratılır. PM emri, kapasite ve bileşen ihtiyaçlarını içeren işlemlerden oluşur. Bakım çalışmasını planlamak için, PM siparişinin terminlenmesi, kapasite ihtiyaçlarının planlanması ve gerekli bileşenlerin zamanında hazır hale getirilmesi gerekir.
Teknik bir nesne, üretimle ilgili bir kaynağa karşılık gelebilir. Bu yüzden PM emriyle bu nesnenin (teknik birim veya ekipman) korunması, onarılması veya kontrol edilmesi aksaklığa neden olabilir. Bu, planlanan bakım süresi boyunca kaynağın üretim için uygun olmadığı anlamına gelir. Üretim planlaması yapılırken bu kesintilerin dikkate alınması gerekir.